All
Switching From Oil or Gas to Heat Pumps
by Shawna Henderson, Blue House Energy
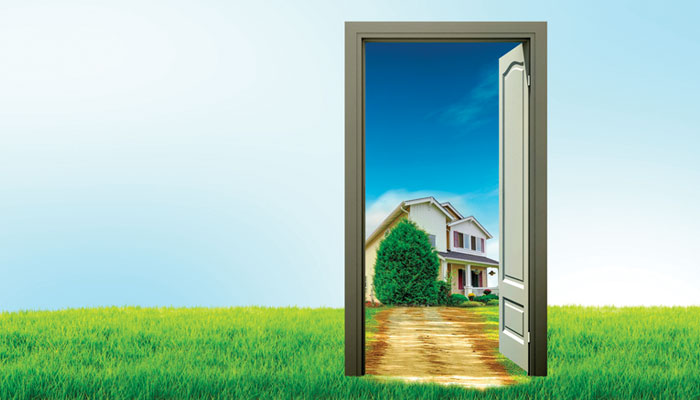
New preferences lead to new opportunities
By Shawna Henderson, Blue House Energy
Historically, my home province of Nova Scotia has many connections with New England, starting with the Planters who settled here way back in the 1760s. Trade ties go back centuries, and some here in the Maritimes argue that the economic ties North and South along the Atlantic coast are stronger than the East-West ties to the rest of Canada.
Boston was essentially the first responder to the disaster that was the Halifax Explosion back in 1917, and for many years, Halifax has sent a specially chosen giant of a Christmas tree to Boston in thanks.
We are also connected by climate, heating requirements and fuel choices. Natural gas as the fuel of choice in Canada essentially stops at the Ontario-Quebec border. Homeowners in the Maritime provinces – New Brunswick, Nova Scotia and Prince Edward Island – along with Newfoundland and Labrador are dependent on fuel oil and electricity for the bulk of their heating requirements.
Homeowners in NS, like those in other areas where oil has been the fuel of choice for decades, are shying away from oil because of the potential environmental damage that can diminish the resale value of a house as well as the insurance premiums on oil tanks and the cost of oil, especially over the past few years. While it looks like there will be a respite from $100-plus/barrel oil prices for the immediate future, it’s hard to know how long that might last, although there certainly are a lot of educated guesses out there.
Regardless of the projections and forecasts of future fuel prices, energy security, rather than economic opportunity, is a central motivating factor here in Nova Scotia, according to a recent report from the Ecology Action Center. The province is almost wholly reliant on import markets for heating, transportation and electricity fuel supplies – a non-enviable and unique position in Canada. In addition, the energy burden on homeowners in Nova Scotia is significant.
Canada’s Energy Efficiency Regulations have required oil furnaces to have a minimum AFUE of 78 percent since 1998. A revision made in 2012 requires oil-fired boilers to have a minimum 84 percent AFUE.
Energy efficiency standards, such as the voluntary R-2000 and Energy Star for New Houses programs, require higher efficiency, direct vent, induced-draft or forced-draft systems with electronic ignition.
Nova Scotia incorporated energy efficiency requirements for the building envelope into its building code in 2010. Provincially, oil-fired appliances (furnace or boiler) are required to have a minimum AFUE of 85 percent in all new installations – whether replacement equipment in existing houses or new builds. Along with the energy efficiency requirements for the building envelope, this has brought new housing up several notches in the province.
Heat Pumps Usher in Electric Heat
In the past few years, however, homeowners were faced with the hard, cold reality that fluctuations in the global market that cause the price to drop rapidly rarely fall in lockstep with the need to fill a tank throughout the season. In fact, in Nova Scotia, while electricity prices shot up 68 percent between 2001 and 2012, oil prices during the same period rocketed by 90 percent.
For many homeowners, incentives and rebate programs driven by a provincial efficiency program with a mandate to reduce electricity consumption have helped make heat pumps a workable solution, both through the incentive and through strong marketing of the efficiency of heat pumps, as well as their bonus cooling capacity.
While oil-fired systems (primarily hot water baseboard delivery) are installed in 70 percent of the existing housing in Nova Scotia, most builders are installing heat pumps in new houses, and many homeowners who are replacing heating systems are leaning towards ductless systems. This is in part due to incentive programs that have favored centrally ducted heat pump systems, including an on-bill payment program offered through Nova Scotia Power, and zero-interest loans that are offered by the provincial ratepayer-supported efficiency organization.
Here in Nova Scotia, coal and oil account for 67 percent of our electrical generation mix, with coal generating the bulk of our power supply. This provides us with one of the highest CO2-equivalent loads per kWh of power generation in Canada – between 1.7 and 2.5 lbs. per kWh, depending on the information source. The remaining 33 percent is supplied by natural gas, wind, hydro, tidal, and biomass. While it may sound like just another interesting tidbit of information floating around in my head, there is a connection to this discussion. Promise.
There’s a lot of hype around the efficiency of heat pumps. That coefficient of performance (COP) – the promise to deliver more heat energy than the electricity used to run it – is easily, and often, misunderstood. The COP is a point-in-time measure at steady state, peak efficiency. The more appropriate metric for choosing a unit is the heating season performance factor (HSPF), which compares the heat produced during the season to the electrical power consumed during the season. In essence, the HSPF is the average COP, which is comparable to the AFUE of a oil-fired unit. The COP is often the metric used to discuss the efficiency of a heat pump.
If you look at the COP of a heat pump versus a high-efficiency oil boiler or furnace out of the context of the generation mix (ah yes, there’s the connection), the heat pump clearly comes out ahead of the oil-fired unit, as the oil-fired unit will always be less than 100 percent efficient, while the heat pump will always be more than 100 percent efficient. But heat pumps don’t operate separately from the grid to which they are attached. The grid is, in fact, the storage tank for the heat pump, and the efficiency with which electricity is generated and transmitted counts in the big picture. When you factor in the generation mix, the efficiency of the heat pump goes down.
Apparent Advantage Is Not There
In Nova Scotia, with the current generation mix, the effect of coal- or oil-fired plants, transmission losses, and other grid-related inefficiencies, a standard-issue heat pump winds up having the same overall efficiency as a high-efficiency oil-fired burner fed by an on-site tank.
Given that a heat pump has an expected life span of over 20 years, and Nova Scotia has made commitments to a high ratio of renewables in the generation mix (25 percent by 2015, fossil-fuel free by 2030), this will change. It would also change if a household rooftop solar electric program were to fall into place in the near or mid-future. Actually, a lot would change if a household rooftop PV program fell into place… ah, let a girl dream.
So while the current generation mix in Nova Scotia discounts the efficiency of a heat pump, the known and unknown factors that will potentially flip that generation mix on its head make heat pumps more interesting to certain market segments that are looking deeper into the future.
Also, heat pump technology has ramped up in the past few years. Heat pumps are a product of a cooling climate, and it’s taken a few rounds to re-engineer them to be geared to a primarily heating climate. The latest generation of ‘cold climate’ units scavenge more available heat in the dead of winter, with improvements and modifications to compressors making them much more functional at lower temperatures. As well, some units have come out with much higher COPs than we’ve seen in the past.
One hurdle that central air-to-air heat pumps can’t leap easily is the fact that in Nova Scotia, the bulk of existing oil-fired systems deliver heat hydronically. Meaning, of course, that switching to a central heat pump means ripping a house apart to install ductwork. Not going to happen often.
Ductless (mini-split) units are often the go-to choice in houses where the oil system is being decommissioned. A rebate/incentive is attached to new centrally ducted heat pump systems only. According to market research, the price point was low enough that homeowners who were making the choice to install ductless units were likely to do so regardless of an incentive.
Where the Business Is
The market reality here is that energy efficiency, based on improvements to the thermal envelope in new and existing housing, is lucrative business, as there are decent rebates and zero-interest loans for air sealing, insulation upgrades and window replacements.
In situations like this, where government policy and incentive/rebate programs are driving market trends towards energy reduction at the envelope and away from oil as a heating source, it really makes sense for contractors whose focus is in oil and gas appliances to think about what they can do to enhance their product and service offering. Here are my thoughts:
- Focus on the benefits of the equipment you offer: high-efficiency, low capacity boilers as replacement equipment for low-efficiency noisy units will always wow the renovation crowd with the projected fuel savings. (Make sure your estimated savings range is achievable!)
- Consider adding an innovative line of equipment: thermal storage units, integrated space and water systems and heat pump water heaters are all proven but still new enough on the market to be considered innovative
- Focus on your team’s ability to consult with builders about optimizing the performance of the house, not just installing high efficiency equipment. Know the comfort and efficiency benefits of home run vs. trunk and branch duct design, the various ways of laying out hydronics, how to size both the equipment and the distribution system for a high-performance house (because it does matter, greatly, as you improve the envelope), and the amount of insulation needed under different types of floor assemblies (slabs, exposed framed floors, etc.)
- Be proactive when it comes to home energy assessments: understand the impact that an envelope improvement has on the sizing of replacement equipment, carry out a heat loss calculation to guide rezoning the delivery side and test that your changes are providing proper comfort levels. (The biggest complaint I get called in about: This room is too hot, but that room is too cold.)
- Reduce callbacks about poor comfort levels that have nothing to do with the equipment you installed/serviced and everything to do with air leakage and lack of insulation. You need someone on call who is good at seeing the whole house picture. Work with home performance contractors who specialize in diagnosing envelope problems, or better yet add an experienced home performance expert to your team. At very least, get somebody on your team trained to diagnose envelope problems so they can speak the same language as a home performance contractor
Related Posts
Burner Questions? The Answer Is in Your Hands.
Posted on April 17, 2024
Carlin Begins Production on UL Listed B100 Burners
Posted on December 7, 2023
NORA Looks at Indoor Air Quality
Posted on December 7, 2023
Why Market Renewable Propane for Your Business?
Posted on October 6, 2023
Enter your email to receive important news and article updates.