All
Matching Curves and Pumps
by Bruce Marshall, Emerson Swan
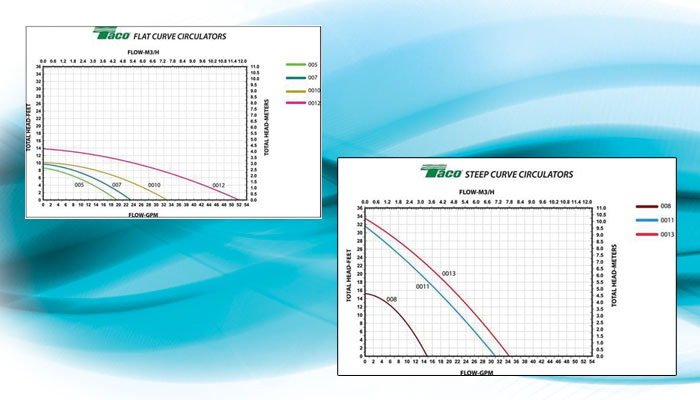
With a little math, a contractor can choose the right pump for the job
When was the last time someone threw you a curve? When was the last time you hit one? We encounter many curves in our lives: curves in the road, learning curves, a popular fitness center for shapely women.
But what about the curves you encounter in your workday, like pump curves? A pump curve is a graphic representation of a pump’s performance based on the manufacturer’s testing.
All pumps work on a curve, based on the horsepower of the pump and the size and shape of the impeller. The curve enables you to see how the pump will perform at any given point within its performance range. The horizontal axis of the graph represents flow rate in either gallons or liters per minute. The vertical axis represents either feet or meters of head.
When selecting a circulator for a particular job, you need to know two factors; the BTUH requirement of the system and the restriction to flow or head loss of the system. This is where the Universal Hydronics Equation comes in.
GPM = BTUh ÷ 8.33 x 60 x 20 (10,000)
The total load of the system divided by 10,000 gives you the GPM requirement of the circulator. Next you need to determine the head loss of the system. Pipes, valves and fittings create resistance to flow or friction head. The standard we use is 4 feet of head per 100 feet of pipe. This number is based on ¾” copper but we can use it for all size pipe. Fittings and valves can account for as much as 50 percent of the total footage of pipe. A good “rule of thumb” shortcut is to calculate the total linear feet of pipe, multiply by 1.5 and multiply that by .04; or even easier; multiply total linear feet by .06. This will take into consideration the 50 percent.
After doing the calculations, we locate the correct point on the pump curve. As long as the point falls inside or on the curve, we know that pump will deliver those BTUs when we need them. It is a good practice not to operate at the extreme opposite ends of a curve, i.e. minimum or maximum. Give yourself about a 10 percent buffer when selecting a pump.
Choice in Curves
There are different types of pump curves that apply to different applications. Flat curve pumps (Figure 1) deliver good flow rates in systems that do not have a lot resistance such as baseboard or cast iron radiator systems. Steep curve pumps (Figure 2) will deliver flow rates against high resistance in systems such as hydro coils, indirect water heaters, radiant systems or condensing boilers. These pumps need to be able to overcome the resistance in the system as well as deliver the required amount of BTUH.
Selecting the correct pump for a given application is critical to the success or failure of the system. For instance, when the system resistance is too great for the pump, the problem will show up at the worst possible time, and that is the coldest part of the season. The system may appear to operate fine in the shoulder seasons because the BTUH load requirement is less. However, when the weather turns cold, the load requirement increases, and if the pump can’t deliver the GPM needed, the immediate effect is insufficient heat. An undersized pump on an indirect will have an effect on the heater’s recovery time. If the tank is drawn down quickly, the recovery time will be much longer than normal, and it will seem like the indirect is at fault when it is actually the pump. A multi-speed pump is a good option in applications such as these because of its ability to choose from three different pump performance curves. By changing speeds the pump curve goes up and the place where the system curve intersects may now be inside and the problem goes away.
Variable Speed Options
In the last few years we have seen an influx of variable speed circulators utilizing ECM technology. Some of these circulators such as Taco’s VR1816 or VT2218, offer infinite variability based on system load changes. These load changes can be either pressure or temperature, Delta P or Delta T.
The main attraction of these variable speed circulators is their effect on energy efficiency in terms of both electrical usage and overall system efficiency. These pumps can use as much as 85 percent less electricity than a split capacitor AC induction motor. And keep in mind that these pumps are currently eligible for sizeable utility rebates.
When sizing these pumps for a job just like any other pump, you must be aware of the range of curves they operate on and make your selection accordingly. Once you understand the dynamics that are going on in a system, you can size and select the right circulator for the job.
Related Posts
Burner Questions? The Answer Is in Your Hands.
Posted on April 17, 2024
Carlin Begins Production on UL Listed B100 Burners
Posted on December 7, 2023
NORA Looks at Indoor Air Quality
Posted on December 7, 2023
Why Market Renewable Propane for Your Business?
Posted on October 6, 2023
Enter your email to receive important news and article updates.