All
Unlike Humans, Fuel Doesn’t Thrive on Oxygen and Water
by Jerome P. Sava, C&S Scientific
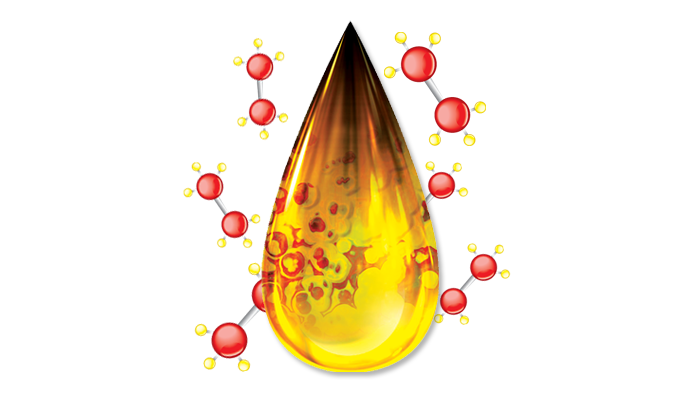
It is ironic that the two essentials for sustaining life—oxygen and water—are exactly those that are entirely unwanted and non-essential when considering the life of stored oil and tanks.
To understand why, let’s start at the refinery. Immediately after crude is refined into fractions such as ULSD and heating oil, these distillates should be free of contaminants such as water, sludge, and bio-organisms. However, even before exiting the refinery, distillates already possess the innate conditions that can later cause significant storage problems – and this is where oxygen and water come into the picture.
Very basically, petroleum is a hydrocarbon fuel consisting of a connected series of hydrogen and carbon atoms bonded together in a variety of individual long chain lengths. During refining, the fuel is subjected to extreme heat and pressure in order to “crack” these chains into shorter lengths. The advantage of cracking is that many fuel types can be simultaneously produced from one crude oil source.
The disadvantage, however, is that cracking creates a fuel with unstable and incomplete hydrogen and carbon bonds, to which oxygen atoms can become attached. When oxygen joins the hydrocarbon chain, it tends to create an oil-insoluble compound that forms a very finely dispersed sediment of gums, resins, and other organics. These compounds agglomerate, thicken, and precipitate to the tank bottom in the form of sludge. In addition to likely sludge problems, oxidation also tends to degrade and destabilize overall fuel quality.
Antioxidant Needed
There probably will never come a time when we can eliminate oxygen from the oil system, but there are fuel-compatible antioxidant components that are available to replace the oxygen at the bonding sites and thereby minimize the adverse effects of oxidation.
Previously the presence of sulfur,
a naturally occurring antioxidant, was often sufficient to slow the oxidation process. However, with negligible sulfur content, the use of antioxidants is increasingly more important. Of course, antioxidants alone will not stop sludge deposition, since other variables invite sludge formations – and this is where the presence of water comes into play.
Water in storage tanks creates a myriad of problems, starting with its ability to form new oil-insoluble compounds in combination with oil. Eventually, these compounds agglomerate, fall out and adhere to any sludge at tank bottom. And that is not all the havoc that water can promote.
In large quantities, water can become entrapped and give the oil a hazy, cloudy appearance. At sub-freezing temperatures, the entrapped water can form ice crystals that will clog filters and shut down the flow of fully liquified fuel oil.
If the fuel should also become supersaturated with water content, a separate water layer will collect at the tank bottom. If close to the suction level, the water may combine with the fuel and degrade fuel economy and performance.
Oxidation and Corrosion
Another area of concern is generalized corrosion of tanks due to oxidation. This is a gradual process, but the presence of a water layer heightens the likelihood for rapid tank corrosion and metal degradation. Acidic organic compounds inherent in the fuel may leach into the water layer and accelerate localized pitting of tank floors and walls. But that’s not all.
The presence of water creates a perfect environment for the culture and growth of bacterial organisms. Fuels contain latent cells of algae, ready to thrive in the right environment, which can form at the oil/water interface, where organisms can breathe oxygen and feed on hydrocarbons.
In the field, these active cells will collect on filters and strainers, another perfect locale for accelerated growth. Eventually residues are formed that combine with sediment to form a slimy, impenetrable obstruction to oil flow.
So, how can we minimize the damage? The first line of defense has been, and always will be, good housekeeping practices. Inspecting tanks for loose caps and manholes, checking the outside of the tanks for any structural flaws, sampling the fuel at various levels to determine uniformity, and periodically sampling the bottom of the tank to identify and, where practical, to remove any contamination buildup. All these measures would serve as the start of an effective maintenance program.
Multi-Function Treatment
The second important line of defense is to be proactive and establish a chemical treatment program that can meet these challenges. This means consistently using a multifunctional fuel conditioner, such as C&S Scientific’s Treat Now, that is formulated with specific components proven to minimize the severity of oil storage problems.
Vital components for multi-function treatment include: antioxidants to slow down the impact of oxidation; stabilizers to prevent co-mingled fuels from stratifying and to stop sludge deposits, neutralizers and passivating agents and prevent corrosion in the tank and line; wetting agents and penetrants to remove existing sludge; water inhibitors to keep fuel clean and moisture free; and anti-foulants to create an environment non-conducive to bioorganic growth.
The results of following these two steps—good housekeeping and consistent use of an effective chemical program—will be the preservation of clean oil tanks and trouble-free, long-term oil storage.
Related Posts
Northeast Liquid Fuel Providers Put Higher Bioblends in Focus
Posted on August 19, 2025
Lower Carbon Lineup Puts Businesses on the Path to Net Zero Goals
Posted on August 18, 2025
Go With the Flow
Posted on July 28, 2025
Why Quality Matters in Your Biofuel Blends
Posted on June 25, 2025
Enter your email to receive important news and article updates.