All
From Truck to Burner
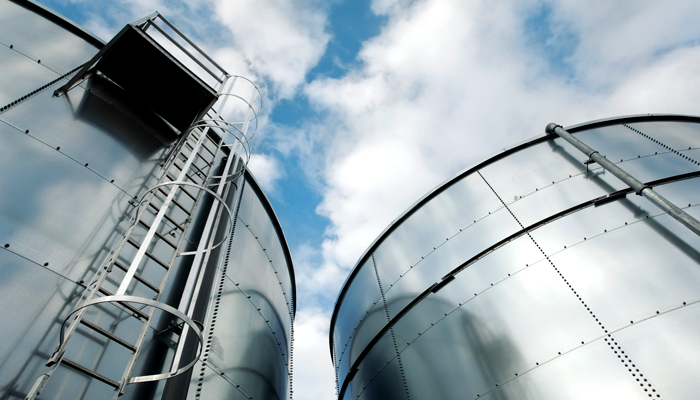
There’s an old example that illustrates fuel destabilization in a scenario familiar to just about everyone. Spring arrives and you go into your garage or shed to take out the lawnmower. You try to start it up, but no matter how hard or how many times you pull the starter rope, it simply will not start. You look in the mower’s gas tank and find it full. So, what happened? Most likely, over the course of the cold winter, the stored fuel’s chemical stability became compromised. Its long-chain molecules broke down, turning the fuel from a light liquid into heavy gunk.
The same thing can happen in heating fuel products. Untreated or improperly managed heating fuel can become destabilized over time. Condensation and sludge in storage tanks can lead to issues like pump failures, leaking gaskets, rusted filter cartridges, plugged filters and lines, leaking fittings, and the list goes on. This has happened with no. 2 heating oil, ultra-low sulfur heating oil and renewable liquid heating fuels.
“Our [fuel] products change daily,” says Jim Todd, a technical sales and support representative with R.W. Beckett Corp speaking to a room of dealers and service technicians at the Eastern Energy Expo. Formerly a delivery driver, service technician, and service manager, Todd has seen firsthand how upstream changes in fuel specifications can impact products downstream and ultimately, the end user. “Manufacturers and refiners work diligently to meet changing standards,” he says. “One follows the other, and the lag period affects us directly in the field.”
Missed the presentation at EEE? Catch it September 18 at the 2019 HEAT Show in Providence, RI. See the full schedule here. Sign up your team here.
To be clear, Todd doesn’t place blame with any particular party or product. Adopting “ULSD is probably one of the best things we’ve done in the industry,” he says. Later he calls renewable liquid heating fuels “the logical investment in the future of the industry, when utilized properly,” adding that biofuels’ solvent properties actually help clean the customer’s storage tank.
Nor does Todd think that fuel dealers are careless when it comes to protecting their customers and the environment – quite the opposite, actually. “If the environmental agencies want to find a group of people who really help the environment, they don’t need to look further than the technicians in this room,” he says. “We proved that with the Montreal Protocol. That hole in the ozone has started to close up, and who did that? You folks right here, through changes in the way you handled air conditioning refrigerants, changes in the refrigerants you use, and changes in your companies’ service policies.”
All of that being said, when it comes to protecting heating fuel throughout its journey from the truck to the burner, Todd stresses the importance of following best practices, and in being proactive rather than reactive. That applies to everyone across the supply chain, from refiners and wholesalers to dealers and service companies, as well as the tank and equipment manufacturers themselves.
Additive Use
“We’ve all seen it,” Todd says of filter plugging caused by destabilization-induced sludge formation. “It looks like chocolate pudding around the tank.” The image provokes a collective head nod from the technicians in attendance. Which, of course, begs the question: if fuel dealers are so familiar with additives, “why don’t more companies use stabilizers?” The answer, Todd says, is cost.
This would be a good place to point out — as Leo Verruso of Advanced Fuel Solutions did during the presentation — that under ASTM specifications for diesel and heating oil, there is no stabilization requirement. However, the ASTM spec for biodiesel does have a stability requirement. Thus, if a fuel dealer sells product blended with BQ-9000® certified biodiesel, that product should have better stabilization properties than an unblended, untreated petroleum product.
With this in mind, it’s important for fuel dealers to know their suppliers and which kinds of additives they’re using. As a fuel makes its way from a pipeline or rail line to a terminal then onto a delivery truck and possibly into another bulk tank before being picked up again for delivery to the end user, there’s plenty of of room for error. Fuel needs to be shipped, stored, and blended properly to avoid contamination.
And even then…
“I can’t speak highly enough of the benefits of stabilizers that are used at an appropriate time frame,” Todd says. He also recommends additives that address microbial growth, which can be accelerated by the presence of water in a tank. Microbiologically influenced corrosion, or MIC, is also thought to result from
the refiners’ sulfur removal processes. (Note: not from low-sulfur or ultra-low sulfur heating oil itself, but rather the process by which the sulfur is removed – a key distinction often left out of the discussion.)
The Clean Diesel Fuel Alliance hypothesizes that MIC occurs when microbial populations degrade ethanol present in diesel to lower-molecular-weight acids. The Renewable Fuels Association challenges this assessment, arguing that ethanol, a gasoline additive, should never come into contact with diesel in the first place. Should. Whatever the cause, MIC can coat surfaces with an accumulation of rust, deteriorating the tank, fouling the fuel product and threatening the residential end user’s heating system.
The best solution, Todd says, is to treat all customers’ tanks, as well as bulk storage tanks, and maximize fuel life by minimizing conditions that would accelerate deterioration.
Tank Care
Of course, residential tanks ought to be properly installed in the first place. According to the National Oilheat Research Alliance, oversized tanks can lead to problems such as poor fuel quality, as larger tanks typically build up more water from condensation.
Thus, it’s recommended that the capacity of a given customer’s tank should represent approximately one-third of that customer’s annual fuel usage. Todd also points out that tanks need to be pitched a quarter-inch to a full foot during installation, or else water will become trapped below the fuel, leading to continual microbial growth that in some cases can only be stopped by flushing out the tank completely.
Outside of the tank itself, all tank piping should be performed up to applicable codes. NFPA 31 calls for pipes to be liquid tight, substantially supported, and protected from physical damage. It should also be mentioned here that copper and its alloys are known to cause reactions with all organic materials, including both petroleum and renewable liquid heating fuels.
Perhaps the biggest oxidation culprit that fuel dealers should look out for, Todd says, is the use of copper or brass dip tubes in storage tanks. Again, this copper reacts not only with the biofuel or additive, but also with no. 2 heating oil itself. As a result, Todd says, even dealers who add detergents and stabilizers to their product “can be left wondering how they’re getting sludge in a tank.”
Finally, and perhaps most obviously, existing tanks should be kept completely free of oxidized metals, and any tank already showing signs of oxidation (i.e., rust) should be quickly inspected, with a replacement recommendation to follow.
“Don’t be ashamed to replace a tank,” Todd advises. While some stigma may surround equipment failures and replacements in America’s heating fuel industry, Todd points out that in the European Union, where biofuel blending is mandated by every member state, some manufacturers’ installation and operations manuals recommend that tanks and systems be replaced as often as every 10 years.
Burner Adjustment
“It’s been a rough couple of years,” Todd says, speaking to the numerous burner issues he and his colleagues have encountered. Among these he cites: seized fuel units, caused by a lack of lubrication; bad pump cutoffs, caused by particulate deposits and surface deterioration; regulator issues, caused by microbe deposits hampering movement in the piston chamber; leaks, stemming from lip seals worn by deposits on the shaft; and priming issues, caused by out-of-spec fuels and sludge accumulation within the fuel unit’s internal passages.
“None of this is a manufacturing issue,” Todd adds, “but we’re still seeing it.” Fortunately, he and many technicians in the field are also seeing ways to proactively address these issues during equipment installation and annual maintenance.
For starters, technicians need to know the size and load on the filter. Two-pipe systems should be sized in accordance with the total gear set capacity – i.e., the amount of fuel the unit will move when it’s on two pipes. Todd says that technicians who find they’re frequently changing filters should ask, “Is it because of the oil or the size of the filter itself?”
He also recommends keeping vacuum ratings, which indicate how much restriction a unit overcomes to deliver the fuel, as low as possible. Specifically, Todd encourages technicians to keep ratings below 6” for a single pipe, below 10” for a single-stage two-pipe setup, and below 15” for two-stage two-pipe configuration.
Even with these practices and others in play, it remains a given that as fuels change so too do combustion results. Still, Todd says, “each generation of biofuel is better” than the last. As for renewable liquid heating fuels and additives in general, he comments, “adding a product to diesel and heating oil that supports combustion is a logical step to reduce our use of hydrocarbon based fuels, and also helps address CO2 emissions.” And as with taking any next “step,” preparation is key.
Related Posts
100 Years of Helping Fuel Retailers Deliver!
Posted on August 18, 2025
U.S. Competing to Secure Critical Minerals
Posted on June 16, 2025
The Clean Air Act, the EPA, and State Regulations
Posted on May 14, 2025
Day Tanks Support Back-up Generators in Extreme Conditions
Posted on March 10, 2025
Enter your email to receive important news and article updates.