All
Scully Signal Co. Focuses on Fuel Delivery
by John MacKenna
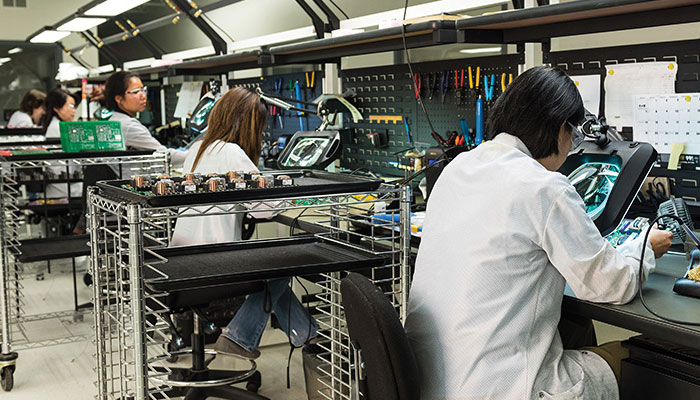
Massachusetts Company has served the petroleum industry since 1935
Anyone who has ever delivered heating oil to a customer’s home has probably used a product from Scully Signal Co., a Wilmington, Mass.-based manufacturer whose focus is squarely on fuel delivery.
The third-generation family-owned business got its start in 1935 when founder Francis P. Scully invented the Ventalarm Signal®, which is the iconic whistling fill alarm that has been mounted on home heating oil tanks everywhere. “No whistle, no fill,” is a safety guideline repeated often in the industry, and it references Scully’s first invention.
Since popularizing the Ventalarm Signal eight decades ago, the company has diversified its product line to meet more of the needs associated with liquid fuel delivery and storage. Scully products are found on storage tanks, on fuel delivery trucks and hoses, and in petroleum terminals.
All the while, the company has maintained a commitment to manufacturing in the United States. Virtually all of Scully Signal Co.’s products are machined and assembled in the Wilmington plant. “We make almost everything except the screws,” said Frank Scully, who handles technical service and sales.
Delivery Specialists
Fuel delivery trucks are a focal point for Scully, according to Katrina Scully Ohl, Director of Marketing and Communications. A single heating oil truck might carry numerous Scully products including the following.
- The Sculmatic® system for controlling the delivery pumping system. It consists of a Mark IV® Flow Control & Check Valve and a throttle actuator;
- Fuel hose components, such as the Sculflow® nozzle or the Super Nozzle ball-valve delivery nozzles and the SuperSwivel for easy hose rotation.
- The Ventafil portable whistle-stop and fill device for underground tanks.
Tank trucks can also be outfitted with sophisticated overfill protection systems that use two-wire or five-wire sensors on each tank compartment and a central onboard control monitor, such as the new IntelliCheck®3.
Scully also meets the needs of petroleum terminal operators, transport fleets and railcar operators for static grounding, overfill protection and vehicle identification at the loading rack. These systems that control hazardous liquids loading of bottom loading and top loading tank trailers and railcars guard against overfill with a combination of sensors on the tanks and controllers in the terminal and on the truck.
The most sophisticated overfill protection systems use a variety of components on the truck, terminal and larger storage tanks to enable efficient loading while virtually eliminating the risk of overfills. The terminal is outfitted with a control monitor such as the Scully Intellitrol®, which connects via a cable and plug to the truck-mounted Scully system on the truck via socket.
When the tank truck arrives at the rack, its overfill protection system is connected to the terminal system through the socket. The liquid level sensors at the top of each compartment automatically signal the controller when the tank is full, or if there is any fault in the system and the controller shuts off the terminal’s fuel pump.
Many bulk plants and tank farms are also fitted with Scully’s electronic high level shut-off systems for storage tank overfill prevention.
All Scully overfill prevention systems incorporate the original patented Dynacheck® circuitry, which checks the system and all internal components 30 times per second to ensure fail-safe operation.
Scully also sells T.I.M. Vehicle Identification Modules that provide the vehicle identification number to the terminal through the overfill protection connection. This enables the terminal operator to positively identify the truck and access all vehicle information on file.
For tank trucks and railcars that load from the top, Scully makes portable cane-type sensors that are manually inserted into the vehicle manhole cover to prevent overfill.
Scully also addresses the need for vehicle grounding at the rack with the Scully Groundhog™ System. When a truck is equipped with the Scully Ground Bolt, the truck can be grounded through the same connection that provides overfill protection. Or, for certain applications where no overfill prevention system is installed, the grounding connection is made via a “smart” Scully Ground Ball on the vehicle and a special ground plug attached to the rack-mounted Groundhog Control Monitor.
Scully offers a variety of systems and components for terminal-to-truck connection to create different performance levels and price points, according to Paul Currie, Technical Service Manager.
Terminals and tank trucks offer new and exciting opportunities for Scully, but the 80-year-old company has not forgotten about the storage tanks that gave founder Francis P. Scully his first opportunity. The company continues to sell the Ventalarm Signal that puts the whistle in heating oil delivery, as well as variations such as the Remote Ventalarm Signal, which provides whistling capability for tanks with lengthy fill lines. Other products include gauges, vent caps, tight fill adaptors, nozzle connectors, compression pipe couplings, and water detectors.
Perhaps the most eye-catching item in the tank equipment line is the Golden Gallon Gauge, which features a glass window that displays large numbers that can be read easily from a distance. The gauge is known for its accuracy and widely used in tanks storing waste oil or lube oil.
All American Company
As a company, Scully is deeply committed to providing local jobs and maintaining quality by engineering and manufacturing in the United States. Virtually every product is designed, created or assembled, and tested at the Wilmington, Mass. plant, which employs about 90 of Scully’s approximately 110 employees. (The company also has sales offices in the United Kingdom and Belgium and sales and service representatives throughout North America.)
Many Scully parts are manufactured from scratch in Wilmington, starting with metal ingots that are melted and die-cast in the factory. The manufacturing operations also include a metal machine shop and onsite circuit board assembly and test in a clean-room section of the plant. Components are assembled into complete products, and that includes the sophisticated electronics that power the IntelliTrol and IntelliCheck systems. Product Development is also handled in-house by Scully’s software, electrical and mechanical engineers.
Scully adheres to a philosophy of supporting all existing products in the field and not forcing customers to upgrade existing equipment unless parts are no longer available or safety is at stake, according to Ohl. Quality and dependability are hallmarks of the company. “It’s not uncommon for our products to outlive the tanks they are installed in,” says Ohl.
“The safety, reliability and efficiency of our customers’ operations is critical to the continued success of our company,” she added. “We are looking providing them with the best fueling solutions for another 80 years.”
Related Posts
Northeast Liquid Fuel Providers Put Higher Bioblends in Focus
Posted on August 19, 2025
Lower Carbon Lineup Puts Businesses on the Path to Net Zero Goals
Posted on August 18, 2025
Go With the Flow
Posted on July 28, 2025
Why Quality Matters in Your Biofuel Blends
Posted on June 25, 2025
Enter your email to receive important news and article updates.