All
Reversal of Fortune
by Bill Holmes, Director of Sales North America, Energy & Transfer Group for PSG
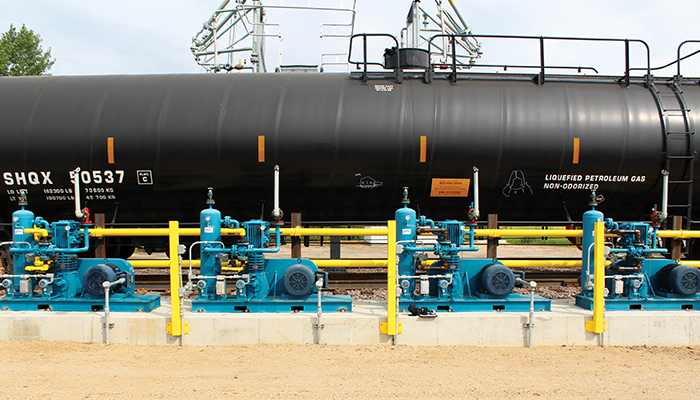
A new era in propane transportation, supply and distribution in Minnesota dawned in May 2012. That’s when Kinder Morgan Energy Partners, L.P., announced the launch of its Cochin Reversal Project, which would see the reconfiguration of its Cochin pipeline from one that supplied propane to the United States and eastern Canada to one that would ship diluents (light condensates/C5/Pentane) from Kankakee County, IL, to the oil sands region of Alberta, Canada.
First placed in service in 1978, the 12-inch, 95,000-barrels-per-day Cochin pipeline was historically used to transport propane and other light hydrocarbon liquids over its 1,900 miles from Fort Saskatchewan, Alberta, to Windsor, Ontario, with intermediate distribution points located in seven U.S. states: North Dakota, Minnesota, Iowa, Illinois, Indiana, Ohio and Michigan. Over the years, the Cochin had become the largest single source of propane supply in Minnesota, with 38 percent of the state’s annual propane supply delivered via the pipeline.
“We use between 400 and 500 million gallons of propane in Minnesota annually. Approximately half of that is used for residential home heat, 40 percent is used for agriculture, and the remaining 10 percent is a mix of commercial, industrial, and motor-fuel applications,” explained Scott McClelland, Engineer at LPG & NH3 Supply, Inc., of Buffalo, MN, which supplies equipment and services for use in the propane market in Minnesota. “When they shut down the Cochin pipeline, it was imperative to find new ways to get propane into the state to keep up with demand.”
Filling The Void
Alliance Energy Services, of North Kansas City, MO, through its subsidiary, Alliance Midstream, LLC, of Benson, MN, which was formed to own, operate, acquire and develop midstream assets used in the transportation and storage of energy products, knew that creative thinking would be required in order to replicate the delivery volumes of propane that would be lost with the Cochin’s reversal.
“Now that the Cochin has ceased the shipment of propane from Canada into the U.S., our industry has a large void in distribution,” Jason Doyle, Founder and President of Alliance Energy Services, said in a July 2014 report in Butane-Propane News. “The area that will be most affected will be the Upper Midwest, and Minnesota is ground zero since it relied on approximately 40 percent of its propane supply from the pipeline. Supplying the market during peak demand periods will be very challenging. The industry must work together, more than ever, to plan and adjust to these distribution challenges.”
Seeing the opportunity to fill the propane-supply niche in the state, Alliance purchased Kinder Morgan’s propane terminal in Benson, MN, which is served by the Cochin pipeline and located about 120 miles west of the Twin Cities near Interstate 94. It was the first major acquisition for Alliance Midstream.
Most of the infrastructure at the Benson terminal was in place, including 17 90,000-gallon propane-storage tanks, which give it a storage capacity of 1.53 million gallons. Alliance determined that in the absence of the Cochin pipeline, rail would be the best way to deliver propane to the facility and constructed a rail spur that would be serviced by BNSF.
“The terminal in Benson has a lot of storage capacity, but we needed a way to get product into the facility,” said Chad Cain, Dealer Account Manager with Alliance Midstream, who helped oversee the build-out of the facility. “Alliance Energy decided the best way to do that was by rail, so we installed the railroad spur off the BNSF mainline.”
As the rail spur was being built, Alliance contracted with LPG & NH3 Supply, Inc., to construct and outfit a propane rack and unloading system that would have the capability to unload up to 16 railcars at a time. With the average LPG railcar possessing a capacity of 33,000 gallons, this would be as much as 530,000 gallons of product flowing into the facility’s storage tanks at once. The propane would be sourced mainly from Canadian suppliers with smaller volumes acquired from the growing production areas in neighboring North Dakota.
“They worked with us to design a system that could unload 16 railcars at a time and get the propane into storage,” recalled McClelland. “What they’ve got now is a large monolithic structure, one long continuous platform with eight unloading stations on each side that can unload eight cars on each side at one time. What’s unique about the setup is that this was an existing pipeline asset that has started filling from rail after they built a rail spur, switch and platform for unloading.”
The site layout was approved by the Army Corps of Engineers in July 2014, with operations commencing before the end of the year, just in time to fill the storage tanks with propane that was to be used in Minnesota’s ultra-important crop-drying and heating seasons.
“We’ve got many carriers that come into the facility,” said Jake Johnson, Transload Operator at the facility. “In one recent week, we unloaded 46 railcars (1.52 million gallons) and had 204 (approximately 2 million gallons) trucks come in. That’s quite a bit of propane considering it’s August and it’s not yet the busy season.”
Lending a Hand
Of all the equipment serving the propane-railcar unloading process, no pieces are more critical than the compressors used to remove the propane from the rail tankers and transfer it into the storage tanks. McClelland had no hesitance in recommending for the task LB942 Series Reciprocating Gas Compressors from Blackmer®, of Grand Rapids, MI, a product brand of PSG®, Oakbrook Terrace, IL, which is a Dover company.
“We’ve got four LB942 compressors total, which are good for unloading two railcars at a time,” said McClelland. “What they’re doing is hooking up the railcars, using the LB942s to unload the liquid and perform vapor recovery. The terminal runs all the time and with those compressors they can turn their 1.5 million gallons of storage, fill it and pump it out, all in 24 hours. They can offload 16 cars in only six or seven hours.”
The LB942 compressors, which feature 30-horsepower motors and the LW mounting configuration, are ideal for the Alliance terminal’s needs because they provide single-stage, oil-free operation and have been designed specifically for propane transfer and vapor recovery with flow rates up to 125 standard cubic feet per minute, which is equivalent to 212 cubic meters an hour or 935 gallons per minute. The compressors are built with pressure gauges, structural steel bases and welded or flanged piping. Additional design features include high-efficiency valves, ductile-iron pistons, self-adjusting piston-rod seals, head and cylinders sealed with O-rings, heavy-duty crankshaft, pressure-lubricated bearing, pressure-assisted piston rings and wear-resistant crosshead assemblies. They also feature ASME liquid traps, which have a mechanical float to protect the compressor by preventing liquid from entering.
“Our Blackmer compressors have to be operating in all weather conditions at all times and be failsafe with no problems, because if we’re shut down we’ve got a line of trucks that are waiting and that just can’t happen,” said Johnson, who is also pleased and impressed that Blackmer products are American-made. “I’m very pleased with the product. They’re very quiet. They run amazingly. We haven’t had any problems. I like Blackmer because I push the button, it’s almost like the commercial, ‘Set it and forget it,’ that’s what it reminds me of. You push the button and it’s going to work all day, no problem.”
With the Blackmer compressors playing a prominent role, the operation has been so successful already that Alliance has purchased some land around the 17-acre facility with an eye toward eventually adding more track to handle more railcars and building additional storage tanks. Any unloading rack or storage additions would also conceivably increase the need for additional Blackmer compressors.
Conclusion
There’s no question that the propane-supply market in Minnesota was knocked for a loop in 2012 when Kinder Morgan announced that the Cochin pipeline would no longer be used to deliver propane. But great change can bring with it great opportunity. Alliance Midstream recognized this and immediately bent to the task of finding a solution to what could have been an overwhelming challenge. The solution—converting the Benson propane terminal into a rail-supplied facility—was a stroke of genius, but the plan could only work if all components were operating to their full effectiveness and reliability.
That includes the compressors that need to operate on a 24/7 basis in order to keep the propane flowing. Alliance’s choice to use Blackmer LB942 Series Reciprocating Gas Compressors for the job has been an inspired one.
“This is the largest propane facility in three states, so everything needs to be state-of-the-art,” said Johnson. “To operate at the level that we are going to operate at, we need top-of-the-line equipment and they spared no expense when they bought those Blackmer compressors. There’s no way they’re going to let us down. They’re like the Energizer Bunny, and I would recommend them to anyone.”
Bill Holmes is Director of Sales North America – Energy & Transfer Group for PSG®, Oakbrook Terrace, IL. Blackmer® is a leading brand of rotary vane and centrifugal pump and reciprocating compressor technologies from PSG. PSG, a Dover company, is comprised of several leading pump brands, including Abaque®, Almatec®, Blackmer®, Ebsray®, EnviroGear®, Griswold™, Mouvex®, Neptune™, Quattroflow™, RedScrew™ and Wilden®. For more information on Blackmer or PSG, visit www.blackmer.com or www.psgdover.com.
Related Posts
What’s Next in Boiler Technology
Posted on June 25, 2025
Data Delivers!
Posted on April 28, 2025
Harnessing Payment Data to Increase Profitability
Posted on March 10, 2025
DeepSeek Is Our AI Wake-Up Call
Posted on March 10, 2025
Enter your email to receive important news and article updates.