All
NREL Report on SAF and Biodiesel Feedstocks
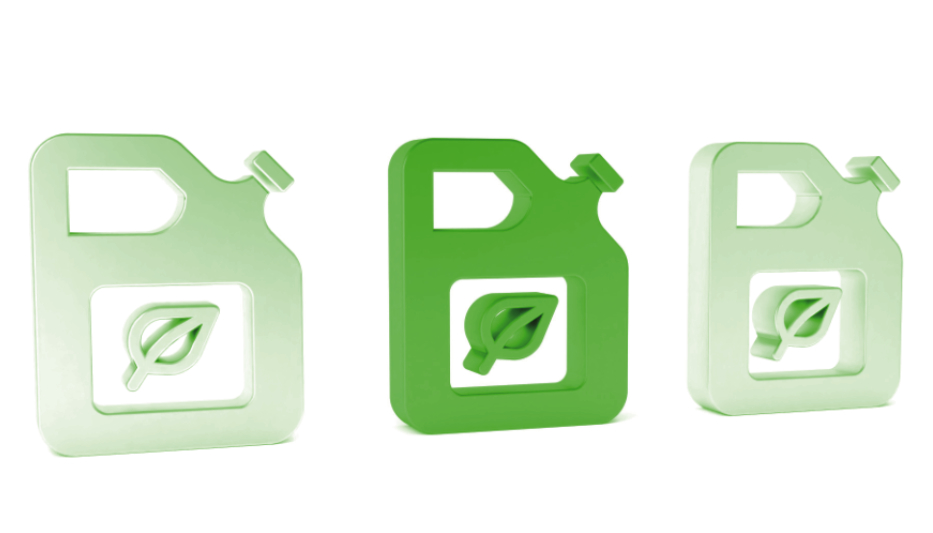
In July, the National Renewable Energy Laboratory (NREL) released its Sustainable Aviation Fuel (SAF) State-of-Industry Report for Hydroprocessed Esters and Fatty Acids (HEFA) Pathway.
The reports center on identifying weak links in the supply chain that have the potential to hinder the production of SAF. The reports focus primarily on hurdles for the 2030 goal of 3 billion gallons per year (BGPY) but also identify some of the challenges to achieving the 2050 goal of 35 BGY.
Currently, the HEFA pathway is the only method commercially deployed to produce significant amounts of SAF. As a result, SAF produced via the HEFA pathway is expected to make the largest contribution to achieving the 2030 production target. This report presents a comprehensive analysis and evaluation of the supply chain, including identification of potential obstacles that could hinder commercial production and use of SAF produced through the HEFA pathway.
The largest issue with using the HEFA pathway to reach SAF goals? Feedstock. (See “Policy Tug-of-War Over Renewable Fuels” in our July issue.)
Multiple industries (including biofuels) in the U.S. utilize the entire 23 million tons of domestic HEFA feedstock produced annually. Due to land use, trade, and infrastructure constraints, it is not anticipated that the U.S. production of HEFA feedstock will increase significantly. Soybean oil, the most abundant HEFA feedstock in the country, accounts for 57 percent of total domestic feedstock production, followed by fats, oils, and greases (FOG) comprising about 28 percent, and corn oil making up roughly 9 percent. The remaining portion of HEFA feedstock is from canola and other vegetable oils. The HEFA SAF industry is severely feedstock constrained and may have to depend on imported feedstock in the near term and work toward developing technologies for alternative feedstocks like algae and oilseed cover crops in the long term.”
All industrial stakeholders identified feedstock supply as a major barrier to scale up production of SAF via the HEFA pathway. These stakeholders mentioned that securing feedstock supply is challenging for plants in operation and for those under construction.
It is important to account for the environmental impact of feedstock production, which can impact availability for fuel producers and end users. Many producers prefer the use of inedible animal fats, sustainably produced resources, or waste materials as part of a circular economy. FOG may be preferred from this perspective, but its generation is linked to human and livestock/poultry population growth. As a result, expected growth is not significant in the future (~33 percent increase by 2050). Cover crops (such as camelina and pennycress) and algae are considered attractive alternatives, as they do not require additional land that would otherwise be used for food and feed production.
From 2012 to 2020, the prices of HEFA feedstocks were relatively flat. However, due to increased renewable fuels production (mainly RD) and limited supply, the prices of HEFA feedstocks have recently increased significantly. It has been projected that soybean oil and FOG prices may moderate depending on market conditions.
In the U.S., the top five states for producing animal fats are Nebraska, Texas, Kansas, Iowa, and North Carolina, while waste greases are processed at various locations across the country. Vegetable oil production facilities are mostly located in Iowa, Illinois, and the North and East regions (including Indiana, Kentucky, Maryland, Ohio, Pennsylvania, and Virginia). Transportation of these materials across long distances to fuel facilities in the West, particularly in states such as California that have low-carbon fuel standards, results in increased carbon intensity (CI) scores and additional logistic expenses for HEFA SAF production.
HEFA Process and Logistics
Industry stakeholders consider the HEFA process a mature technology that entails some technical challenges in scaling up SAF production, but technology is not considered a major barrier.
HEFA feedstocks require pretreatment to meet the quality standards for the HEFA process. Pretreatment makes it possible to use cheaper, lower-quality raw materials, reducing production costs and adding flexibility in processing a variety of oil-based feedstocks. For repurposed petroleum refinery equipment, challenges include controlling the reactor temperature, reducing unit capacity (maintaining only 25–50 percent of the original unit capacity), new catalysts for renewable feedstocks, additional separation infrastructure, space/footprint availability, and other investment requirements. Many of these challenges can be addressed a priori in greenfield units. Repurposing fossil fuel petroleum refineries to oxygenated feedstocks will generally result in derating nameplate production capacity.
Building new HEFA SAF facilities or repurposing petroleum refineries can take anywhere from 2 to 5 years. This could make it challenging to meet the 2030 SAF production objectives. Although coprocessing renewable streams with fossil streams can speed up SAF production while minimizing capital expenditures, SAF production through HEFA coprocessing is limited to a maximum of 5 percent cofeed of HEFA feedstocks. ASTM is currently considering increasing the HEFA coprocessing limit to 30 percent to improve the cost efficiency of using refinery equipment, as well as other incentives. In 2023, an additional coprocessing option, termed here as fractionation coprocessing, was approved, which enables the blending of up to 24 percent previously hydroprocessed biomass intermediate streams with a petroleum stream in traditional refineries to generate a jet fuel blend containing up to 10 percent renewable hydrocarbons (ASTM D1655-23. Annex A1.2.2.3).
While the pathways for SAF and RD are similar, conditioning an RD facility for producing HEFA SAF might not be immediate and could require additional processing steps and investment. Specifically, more severe isomerization and hydrocracking are necessary to achieve jet fuel’s cold-flow specifications. In addition, SAF yields are typically lower than RD yields, necessitating adjustments to the fractionation units, the adoption of alternative methods to maximize production, and an increased demand for hydrogen. RD systems may not have sufficient fractionation capabilities, but this is required for SAF production.
Additional Inputs Required for the HEFA Pathway
Sourcing hydrogen is a major challenge for HEFA SAF facilities. Hydrogen needs are significantly higher than for fossil jet production, between 2 and 19 times more per gallon of fuel produced. Concerns have been raised by industry stakeholders regarding the potential difficulties for refineries to obtain sufficient hydrogen. Some feedstocks such as palm oil will require renewable hydrogen to meet the GHG emissions reductions targets under the SAF Grand Challenge. If a refinery does not have sufficient hydrogen capacity, the use of HEFA processing may be limited.
The source of hydrogen has a significant impact on its CI score, which in turn affects the eligibility of the fuel for incentives. Some industry stakeholders are concerned about the availability and costs of hydrogen produced through electrolysis using renewable electricity. Though it has a lower CI score, this is a relatively new commercial-scale technology that requires a significant capital investment and renewable electricity.
Policies, Permitting, and Approvals Impacting the HEFA SAF Supply Chain
Industry stakeholders have identified durable policies as key barriers to reaching SAF production targets. Current policy slightly favors RD.
The Inflation Reduction Act (IRA) allows two complementary schemes for generation of SAF and RD fuel credits in the 2023–2024 time-frame, and from 2025–2027 they merge into the Clean Fuel Production Credit.
Industry stakeholders have identified permitting as a crucial factor for constructing RD and HEFA SAF facilities. Thus, the permitting process needs to be streamlined and community engagement needs to be enhanced.
Economics and Sustainability of the HEFA Pathway
Industry stakeholders raised concerns about the elevated selling prices of SAF in the market. They see the slow development of the SAF industry as an indication of the price difference between the high production cost (which results in high selling price) of SAF and the market price for Jet A.
The minimum fuel selling prices (MFSPs) of HEFA SAF estimated in this report range from $1.84 per gasoline gallon equivalent (GGE) to $9.40/GGE for all scenarios considered. The MFSPs of RD are slightly lower than those of SAF. As a reference point, the prices (sales to end users, exclusive of taxes) of fossil-based jet fuel and diesel in California in 2021 were $1.85/GGE and $2.36/GGE, respectively.
By factoring in GHG emissions reductions and the incentive amount for which a given fuel qualifies, the return on invested capital (ROIC) is calculated based on market value (MV) only (not including incentives) and MV plus revenue from federal and state incentives. Total revenues, including incentives, for several cases were greater than production costs, showing profitability potential assuming the jet fuel market price is at $2.50/gal (wholesale, spot price, equivalent to $80/bbl West Texas Intermediate).
MV ROIC (based only on MV revenue) is negative for RD and SAF production for all feedstocks except yellow grease, which has a slightly positive MV ROIC. By factoring in the GHG emissions reductions and the amount of incentive that the fuel qualifies for, the ROICs after federal and state incentives (using California as an example) can be significantly increased. ROICs after incentives are positive for both RD and SAF, except for palm oil-derived SAF and HEFA coprocessing-produced canola oil-derived SAF.
The ROICs after incentives suggest that producing RD is preferable to producing HEFA SAF. Today, RD is being priced as a commodity fuel blendstock and SAF remains a niche product at current production volumes.
Policy incentives increase significantly when CI is reduced. Although sourcing hydrogen from water electrolysis with renewable electricity instead of natural gas reduces CI by at least 10 percent, some industry stakeholders view electrolytic hydrogen technologies as too expensive and not yet widely available enough to prove viable. Results suggest that incentives partially offset additional costs for sourcing hydrogen via electrolysis, but no incentives entirely cover additional costs.
Related Posts
Northeast Liquid Fuel Providers Put Higher Bioblends in Focus
Posted on August 19, 2025
Lower Carbon Lineup Puts Businesses on the Path to Net Zero Goals
Posted on August 18, 2025
Go With the Flow
Posted on July 28, 2025
Why Quality Matters in Your Biofuel Blends
Posted on June 25, 2025
Enter your email to receive important news and article updates.