All
Measuring Quality Beyond the Gallon
by Paul Nazzaro, President, Advanced Fuel Solutions, Inc.
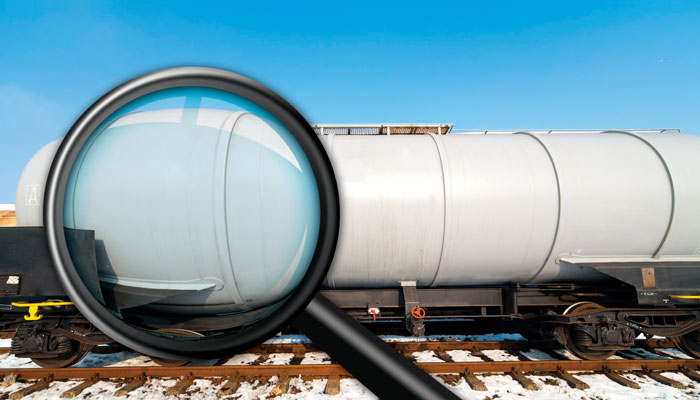
Paul Nazzaro discusses fuel treatment
Are the fuels that you sell similar to when you started your distribution business? Do you receive consistent quality from one supplier to the next, and are you able to identify any differences?
Generally speaking, diesel fuel was developed in the mid-1920s to meet the growing demands of that period’s diesel engines and vehicles. Interestingly we are now witnessing a similar renaissance, as fuel injector manufacturers continue meeting the demands of policy makers to deliver cleaner air and improved fuel economy. Simultaneously the home heating industry continues transitioning to lower sulfur fuels, which will help decrease the consequences of sulfur’s impact on the systems heat exchanger.
From the beginning, diesel fuel had always maintained high sulfur content. Then in 1993, the Environmental Protection Agency (EPA) mandated that all diesel fuels should be low-sulfur. Ultra Low-sulfur would be designated by 500 ppm. By June 1, 2006 EPA again mandated all diesel fuel intended for on-road use should be ultra-low-sulfur diesel (ULSD), designated 15 ppm. Then in 2011, all diesel produced in the U.S. was mandated to be ULSD, whether they were intended for on or off-road use.
Diesel Is Different
Although ULSD is a much cleaner fuel, this reduction in emissions comes with tradeoffs. Did you know ULSD contains fewer BTUs than high-sulfur fuel due to the impact of refining; this can result in a lack of performance. Another side effect of lower-sulfur fuel is that older injection systems will suffer, as will oil burner pumps due to lower lubricity. Less sulfur indirectly means reduced lubrication, and reduced lubrication deprives systems of maximum life expectancy. Many think that it’s the sulfur itself that was the driver for lubricity, but it is actually the process of removing the sulfur that compromises this quality parameter.
The vast majority of the older fuel systems on our roads today were designed for low sulfur fuels, not ULSD. If you are concerned about your older diesel equipment it would make sense to consider optimizing the fuel that you sell through an intelligently managed treatment program that addresses lubricity and other factors. However, since ASTM has adopted a lubricity specification under D975, you can be assured that regional wholesalers address the limits defined under ASTM D975 by adding lubricity additive prior to the fuel leaving the rack.
The next point to discuss, especially at this time of year, is a fuel’s ability to perform throughout the winter. Whether operating a truck or heating a home, fuels need attention to determine how they will perform in cold temperatures. Have you ever put a winterized blend of diesel fuel in your equipment or taken an order from your customer for a 70/30 kerosene blend? Winterized fuels can be a blend of No. 1 diesel and No. 2, with No. 1 having a higher volatility than the No. 2. Not only can winterized fuel atomize better, turning from liquid to vapor easier, but it also has a lower cloud point which can minimize gelling in colder temperatures.
Blend for Your Climate
A sound approach to consider for achieving optimal winter protection is blending properly engineered cold flow additives with approximately 20 percent kerosene, (depending on where you are buying and selling). Additives are not designed to depress the cloud point but will alter the wax crystals’ growth, keeping the wax crystals microscopic so that they flow through tight filtration into combustion.
In the most challenging winter geographies, buyers and sellers have learned to combine these two strategies to achieve optimum winter performance. Noted compromises associated with kerosene blending include supply constraints and pricing differentials between kerosene and diesel. At times these differentials can make blending financially intolerable.
Not often discussed is how the supply chain functions, or simply put, how does the fuel that you buy and sell get to the regional terminal? I would never debate successful fuel dealers that suggest it’s more convenient to load their trucks at the market close predicated on cost, credit lines, and terminal access than it might be on the quality of fuel itself. What I am encouraging dealers to do is to become diligent in understanding the products which they sell and not necessarily to think about commoditizing it out of the box.
As a reminder about where your gallon starts before you pull it from the rack you need to look over your shoulder all the way back to the refinery. Crude oil is gathered and sent to a refinery to be processed into finished gasoline, diesel and heating oil, all of which meet minimum ASTM specifications. Extreme production processes, high temperatures, chemical agents, pressures and catalysts are relied upon to achieve the refiners’ production goals.
Once produced, the product traverses the nation by pipelines, ships, barges, truck and railcars to be stored in field-constructed tanks somewhere in the United States. This is the end of the line for this single gallon of distillate that awaits pickup for distribution to the most valuable link in the chain, the consumer.
The Final Stop
The product’s final stop can be a 275- or a 20,000-gallon storage tank. While product sits awaiting use it can and will prematurely age. During this process the sedimentation commonly lurking on the bottom of the tank rears its head after the velocity of the fuel delivery aerates the tank. Air breathing elements can be installed to protect the tank from airborne contaminants and moisture that is guaranteed to hassle fuel performance. This is the beginning of what “measuring fuel quality beyond the gallon” means.
No one is suggesting that suppliers sell inferior fuel; they don’t. They deliver to the market an ASTM minimum specified fuel, which you must manage to ensure it remains on specification through the consumption phase of this transaction.
We can intelligently discuss and rationalize the value associated with offering your customers fuels that rank higher than “minimum specification” qualities, but to truly discuss quality the focus needs to go beyond the gallon itself and into all storage, handling and distribution practices supporting the fuels that you buy and sell.
Our industry is driven by policy that demands equipment manufacturers adhere to requirements to optimize equipment for efficiency and operational superiority. It’s safe to say that more changes are on the way, changes that may be far more radical than those which we currently comply. Are you prepared for these changes?
Related Posts
Why Quality Matters in Your Biofuel Blends
Posted on June 25, 2025
Incorporating Higher Blends of Biofuels
Posted on May 14, 2025
NORA Programs at Eastern Energy Expo
Posted on May 13, 2025
March Short-Term Energy Outlook
Posted on April 28, 2025
Enter your email to receive important news and article updates.