All
Keeping Water Out of Storage Tanks
by Jason Lawrence, Chevron Renewable Energy Group
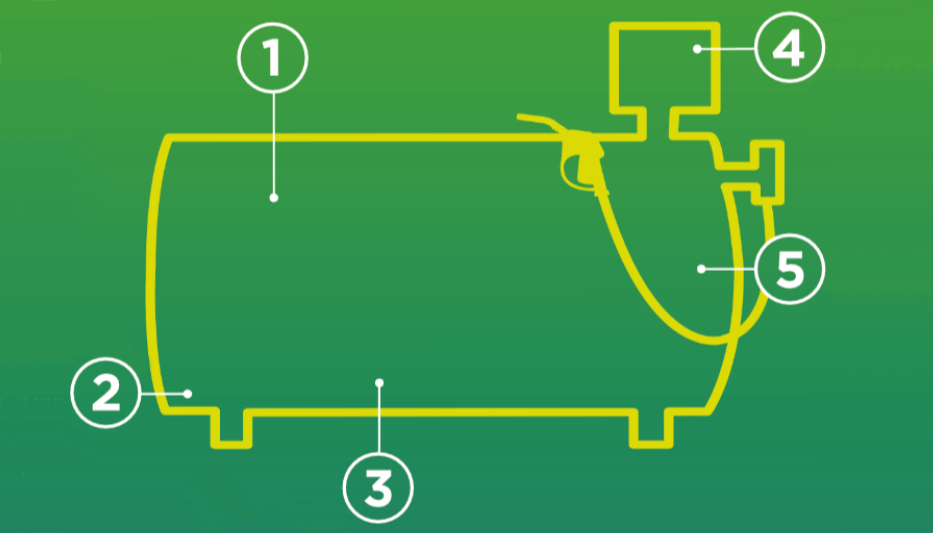
How do you prevent water, corrosion and microbe issues in fuel tanks? Hint: It’s not the fuel.
Biodiesel does not cause water issues in fuel tanks. Let’s get that out of the way. You may have heard differently, but the truth is that water is everywhere in our environment and is a concern with all fuels. That’s why storing fuel — be it petroleum diesel, renewable diesel, biodiesel, gasoline, fuel blends or jet fuel — in a clean, dry tank is critical. In fact, water is the common denominator for two major issues with fuel storage: microbial contamination and corrosion. Let’s address these one at a time.
Water — No fuel can create water, including biodiesel. Also, dissolved water isn’t the issue — free water is the problem. If there’s a way for free water to get into any fuel tank, it will be there. Sources of free water include rain, mist, fog and condensation from combinations of warm days and cool evenings or warm air above ground and cool underground temperatures. Once a fuel tank has free water in it, it is likely to cause issues, one of which is microbial growth.
Microbial contamination — Free water is the root cause for microbial activity in tanks. Sulfur compounds historically acted as antimicrobial agents, which wasn’t fully realized until lower sulfur levels in ultra-low sulfur diesel (ULSD) were observed to allow more microbial growth. Biodiesel has received some of the blame simply because its use became more widespread at the same time ULSD was introduced. However, the temperature and chemical environments in the pipes and vessels in biodiesel production processes actually inhibit microbial growth. Also, biodiesel storage tanks and transport loads are less likely to contain free water than petroleum products. The outside world is full of microbes in the air, dirt and surface water, which means some microbes will always be present in an underground fuel tank. But that presence alone doesn’t cause the problems, the problems occur when microbes are allowed to reproduce and flourish. This requires a free water layer in the bottom of a tank and time for the microbial population to grow unchecked.
Corrosion — Excessive microbial growth can contribute to corrosion in a storage tank (remember, this requires the presence of free water). Any kind of fuel can act as a growth medium for these microorganisms. They live in the water layer, eat fuel molecules and some can excrete corrosive molecules such as acetic acid. Corrosive molecules can affect tank walls, pipes, fittings and pump parts, and can cause rust to accumulate in dispenser filters.
Clean, dry tanks are important to help your systems run properly. Here are five tips to assist with keeping your tanks clean and minimizing the chances of water getting into the tank.
- Take a dispenser sample at least every 30 days and, ideally, immediately after a fuel delivery when the tank bottoms have been disturbed.
- Periodically pull samples from the dead bottom of the tank and inspect for free water and hazy fuel.
- If free water problems persist for more than a week, consider removing water and wet fuel from the bottom of the tank and treating the tank with a biocide additive.
- Evaluate your system for potential points of entry for water and monitor regularly.
- Consider automated water-detection systems, if possible, to provide continuous monitoring in addition to periodic sampling.
Chevron Renewable Energy Group understands minimizing tank corrosion is important. That’s why we educate customers on the potential impacts of free water in a fuel tank, and our technical services team is ready to help. These laboratory technicians, chemists and engineers, based in Ames, Iowa, and Amsterdam, lead quality efforts including performing many fuel tests for customers and non-customers alike, and often at no charge.
The technical services team provides advice on storing, handling and blending fuel, and offers testing including:
- Cold Soak Filtration, Cold Soak Filter Blocking Tendency, Cold Filter Plugging Point (CFPP) and Cloud Point testing to determine cold weather properties
- Elemental analysis, such as Inductively Coupled Plasma (ICP) testing, to identify and quantify elements other than carbon, hydrogen, and oxygen, such as sulfur and metals
- Gas Chromatography (GC), GC-Mass Spectrometry (GCMS) and GC Headspace testing to identify and analyze different substances in a liquid sample
- Fourier-Transform Infrared Spectroscopy (FTIR) to determine the presence of a wide variety of molecules and materials in liquid and solid samples
- Viscosity, density, flash point and energy content testing.
Chevron Renewable Energy Group provides regular updates on its biofuels and bioblends with the “Let’s Blend” monthly e-letter. Subscribe online at www.regi.com/newsletter to keep current with the company, its advancements in renewable liquid heating fuels and more.
Jason Lawrence is Senior Business Development Executive at Chevron Renewable Energy Group. He can be reached at (717) 989-1313 or jason.lawrence@chevron.com.
Related Posts
Why Quality Matters in Your Biofuel Blends
Posted on June 25, 2025
Incorporating Higher Blends of Biofuels
Posted on May 14, 2025
NORA Programs at Eastern Energy Expo
Posted on May 13, 2025
March Short-Term Energy Outlook
Posted on April 28, 2025
Enter your email to receive important news and article updates.