All
How Tank Monitors And Other Tech Maximize Delivery Efficiency
by Farid Widjaya
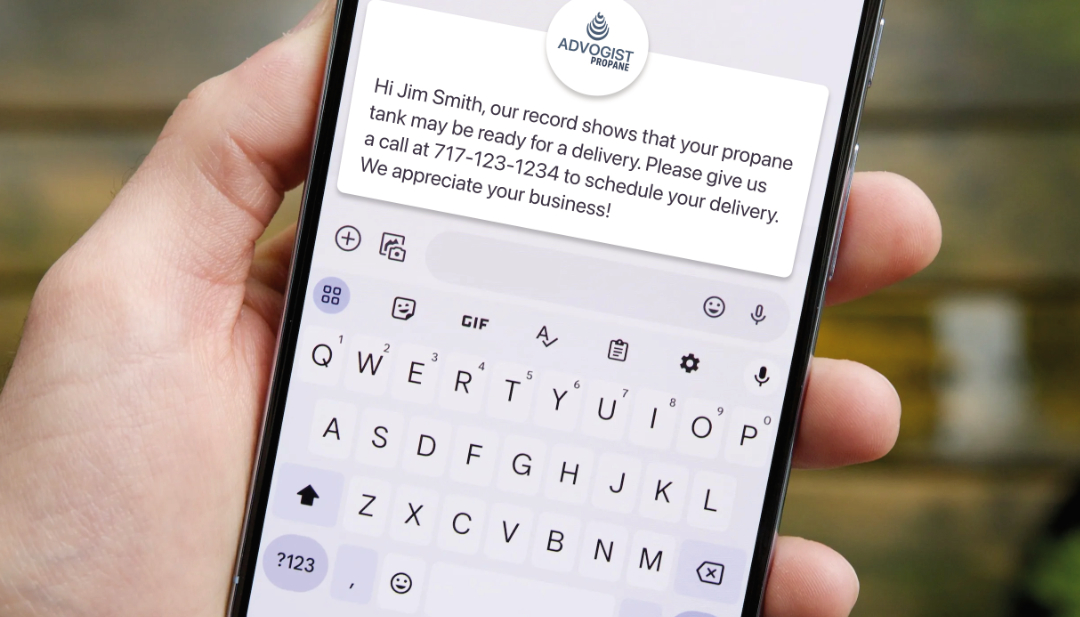
Internet-connected tank monitors remotely measure fuel levels in real time.
The Rise of Tank Monitors
Tank monitors have been around for years and have only grown in popularity as adoption has been made easier and more affordable. In fact, almost 70 percent of respondents to Cargas Energy’s 2024 Top Technology Trends in Fuel Delivery report deployed or spent more on tank monitors in 2023 alone. Here’s what makes tank monitors so powerful on their own:
Accurate Tank Level Readings
Forecasting with K factors and historical data was once the most reliable way to determine delivery needs—but this method wasn’t that reliable. Why? There’s simply no way to keep clean, historically accurate data in the fuel delivery industry, where companies have decades’ worth of data from well before the age of computers and the potential for error after countless system changes. Add in age-old variables of usage, weather patterns, and individual home efficiency, and forecasting becomes a guessing game.
This veritable variable storm gave delivery companies two options—wait and risk a runout, or deliver and check tank levels more frequently at the risk of smaller drops and overwhelmed drivers.
Tank monitors changed the game by eliminating guesswork and giving dispatchers a snapshot of the customers who need fuel the most.
More Delivery Flexibility
Fuel dealers set an optimal fill for a tank based on the tank’s volume. For instance, a 275-gallon tank might have an optimal fill of 60 percent, meaning it should be refilled when it hits 110 gallons. The goal is to let the fuel reach a level that is high enough to keep the customer comfortable, but low enough that the delivery company can maximize gallons delivered.
In the forecasting age, fuel dealers who saw frequent runouts came to distrust their own data. The result? A lower optimal fill level and less efficiency.
Tank monitors streamline routes by giving dispatchers the exact information they need. They can see when tanks are “in the red” and more reliably predict how upcoming weather patterns may impact that number.
Diverse Delivery Areas
Forecasting was made complicated by fluctuating weather and seasonal usage. Tank levels in dry, temperate climates weren’t too difficult to forecast. However, variables made prediction accuracy challenging for tanks in summer cabins or regions with severe weather patterns and temperature changes.
With tank monitors, it doesn’t matter where the tank is or how often it’s used; all that matters is the fuel level left in the tank. Dispatchers don’t have to worry about seasonality, nor’easters, or cold fronts, just who needs fuel and when.
Owning the Office with Tank Monitors
Implementing tank monitors is a significant benefit for fuel delivery companies, but it’s still the first step of a much larger strategy. The true power of tank monitors can only be unlocked when paired with other modern technologies.
The Back-Office System
The process of migrating tanks to a remote monitoring system can be costly and expensive, especially for larger outfits. Often, organizations that use tank monitors must juggle both monitored and non-monitored customers. Without a way to bring tank monitor readings into the back-office system, data is spread out and difficult to manage. Back-office systems centralize this data so dispatchers can see each tank, regardless of whether it’s monitored, and build the most efficient routes for all customers.
Customer Experience
When integrated with communications tools such as texting modules and automatic email sends, tank monitors can play a role in customer retention, particularly for will-call customers. Will-calls are on the rise as customers demand more control over the fuel-buying process.
Monitors on customer tanks tell fuel dealers exactly when they need a delivery, which means the company accessing that remote data can send automatic reminders and alerts. This keeps the company top-of-mind for will-call customers when it’s time to fill a tank. And, more broadly, it gives customers the power to make the purchase on their terms.
The Key Is Connection
With tank monitor usage at an all-time high, it’s important for fuel dealers to make sure they are getting the most out of their investment. The key is integration—tank monitors have a vital role in the back-office, but to truly own the office, propane, and heating oil delivery companies must use an interconnected network of solutions that share data to streamline business processes and keep customers happy, comfortable, and safe.
Farid Widjaya is the Energy Product Marketer at Cargas, and he has been with the company since 2008. Farid helped develop the user interface for Cargas Energy and has assisted with data conversions, project implementations, and technical support. Today, Farid has served as a liaison between the Product and Marketing teams, using his expertise to plan go-to-market strategies and act as a brand ambassador.
Related Posts
How Advanced Financial Analytics Can Fuel Your Energy Business
Posted on August 15, 2025
Why Cash Flow Optimization is the Key to Profitability for Fuel Companies
Posted on July 28, 2025
Safety and Security: Are You Staying Ahead of the Game?
Posted on July 28, 2025
8 Strategies for Effective Wealth Transfer in a Business Succession
Posted on June 16, 2025
Enter your email to receive important news and article updates.