All
Fuel Transition Brings Challenges
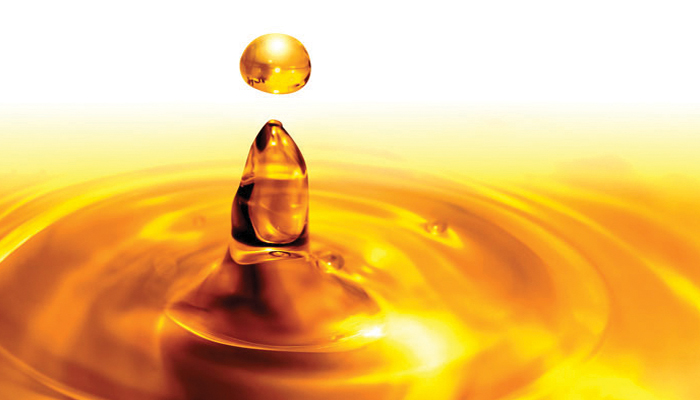
As the heating oil industry continues its gradual march toward ultra low sulfur, fuel marketers must be ever more vigilant about protecting tanks and other equipment, according to fuel and tank experts.
Energy marketers who distribute on-road and off-road diesel are already familiar with the problems associated with reduced sulfur fuel, because those distillate products were transitioned by federal mandate to 15 parts per million (ppm) or ultra low sulfur diesel (ULSD) between 2006 and 2010.
Those mandates did not address heating oil, and the state heating oil associations had to lobby for state laws to reduce sulfur and help heating oil compete in markets where emission levels are under intense scrutiny.
The state-by-state approach led to an uneven transition, with some states mandating sulfur reductions before others. New York State led the way by switching to ultra low sulfur heating oil (ULSHO) in 2012. Since then, eight other states have either switched to ultra low or to a transitional 500ppm fuel. The transition will be mostly complete in 2018, when the six New England states and the District of Columbia switch to ULSHO.
Corrosion Risks
The environmental and competitive benefits of reducing sulfur are clear, but there are potential consequences. Reduced sulfur fuel seems to be more corrosive, which creates the potential for damage to tanks and fuel-dispensing equipment, as has been witnessed with on-road and off-road diesel. The petroleum fuels are also being blended with biodiesel, which brings its own set of challenges.
Brian Savage, President of Savage Associates, experts in liquid fuel storage and handling, said the newer fuels are more susceptible to contamination by bacteria and the formation of acetic acid. He believes fuel issues are complicated by “switch loading” of fuel trucks between gasoline and heating oil, which introduces ethanol from the gasoline stream into the heating oil, where it accelerates the formation of moisture and bacteria.
The sulfur in heating oil has helped to retard bacteria formation, but as sulfur levels drop, bacterial problems can increase, leading to the formation of highly corrosive acetic acid. “Ultra low sulfur is a lot more bacteria-friendly,” Savage said. Fuel storage experts are increasingly using fuel-drying strategies to eliminate water, including filters that remove the water before the fuel goes into storage.
Mark Stellmach, President of Fuel Management Services, says awareness is growing in the heating oil market. “We should look at what other markets have experienced and use it as a blueprint so that we do not suffer through the same problems,” he said.
He recommends that marketers routinely monitor their tanks and their customers’ tanks for water accumulation. Tanks in a bulk plant can be outfitted with water alarms, while residential tanks can be checked with water-finder paste. When they detect water in a customer’s tank, marketers can use a water sock to absorb and remove it. Stellmach also recommends using additives that contain a demulsifier that causes the water to separate and precipitate out of the fuel. “The days of lax housekeeping on storage systems are over,” he said.
Mind the Sediment
Paul Nazzaro, President of Advanced Fuel Solutions, said that liquid fuels have always had the potential to cause corrosion, and treating fuels to inhibit corrosion remains a sound practice.
While acknowledging the potential for problems stemming from sulfur reduction, Nazzaro says that the bigger issue for heating oil retailers is sedimentation in customers’ tanks. Sediment comes out of the fuel over time and settles, only to be agitated whenever the tank is filled. When larger particles of sediment move with the fuel, there is risk that nozzles and fuel filters will plug.
Many factors are threatening fuel quality in the customer tank, according to Nazzaro. Tanks are rarely full, which means there is a void inside the tank where moisture can form. The fuel might also have excess salinity due to desulfurization processes at refineries. Marketers can minimize problems by using additives that combine dispersants, corrosion inhibitors, stabilizers and metal deactivators.
Related Posts
Why Quality Matters in Your Biofuel Blends
Posted on June 25, 2025
Incorporating Higher Blends of Biofuels
Posted on May 14, 2025
NORA Programs at Eastern Energy Expo
Posted on May 13, 2025
March Short-Term Energy Outlook
Posted on April 28, 2025
Enter your email to receive important news and article updates.