All
Forging a Stronger Supply Chain
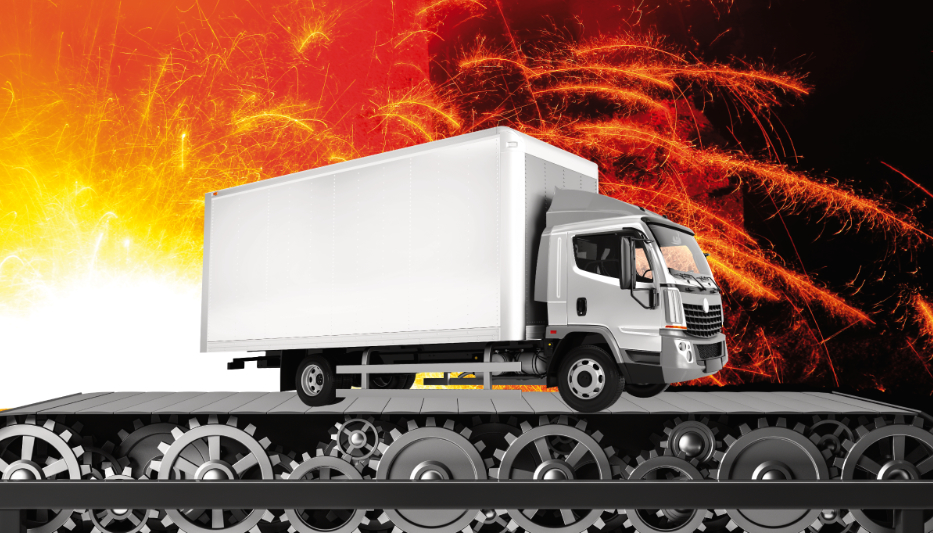
All systems are pointing to go for equipment wholesalers, installers and repair services
Is the light at the end of the tunnel an on-time truckload of equipment?
It’s been a long haul. Pandemic shutdowns, backorder bottlenecks, driver shortages and shipping snafus. Warehouse managers of all sizes had to deal with logistics logjams, the likes of which no one had seen, on one hand, and frantic service and installation departments, company leadership and end-users on the other.
Finally, things appeared to be returning to a semblance of normal, until this summer, when UPS drivers and FedEx pilots threatened strikes and Yellow, one of the country’s oldest and largest less-than-truckload (LTL) shippers, folded.
At the time of this writing, UPS and its drivers had reached an agreement and the FedEx pilot strike is too far in the future to be of concern. The Air Line Pilots Association is covered by the Railway Labor Act, and as such must receive Congressional permission to strike after federally mediated negotiations fail. A strike, therefore, is unlikely for quite some time. As a point of reference, the railroad workers union began negotiations in November 2019 and didn’t call for a strike until the summer of 2022 – at which point Congress stepped in.
That’s two crises averted. As for Yellow folding, other LTL company leaders speaking to Transport Topics News were professional enough to not sound giddy at the thought of the increased business and higher prices that would be coming their way. Analysts and owners agree that there is enough capacity to absorb the Yellow freight, especially as the shipping sector had been soft in the second and third quarters.
Does that mean things are back to normal? The answer appears to be a qualified “yes.” One equipment manufacturer noted that they weren’t experiencing the raw material, electronic component and plastics shortages that they had to work around during COVID, adding that their on-time downstream delivery metrics were over 98 percent, a record which would not be possible if there were supply chain issues on the production end. Another manufacturer replied that while there are still the occasional late orders – and when are there not – they’ve been able to sustain their capabilities as well.
Where We Are Now
About 18 months ago (April 2022), Oil & Energy spoke with Andy Stearns, Director of Purchasing at propane equipment wholesaler Bergquist Inc. To see if – or how – things have changed, we checked back in with Stearns.
“The last time we spoke, everyone was readjusting and figuring out the changes that needed to be made internally because of the way the pandemic affected the supply chain. We worked with suppliers, vendors and customers. Kept them as informed as we could, shared information. Everyone was dealing with the same situations: product shortages, longer lead times, raw materials issues. Where we’re at now is way better than where we were before. We all learned how to deal with it.”
No situation or system is foolproof, but, he says, “There are still some things, depending on the material or item, that you might still struggle with, but it’s gotten much better. Credit that to the relationships we have. When something happens, like a strike or shipping issue, it could directly affect our supply, or indirectly affect it. It’s a ripple effect. But it all goes back to the relationships we’ve had since we started. We let our suppliers know what we need. At the customer level, we’re as transparent as possible. So, if a one-week lead time becomes four weeks, and it’s because of a product shortage, we give them updates and they know we’re doing our part.”
Stearns insists that the company was prepared for the UPS strike that didn’t happen, and that Steve Eide, their Vice President of Distribution and Warehousing, had enough carrier, product and vendor diversity to creatively weather any shipping issues that might have arisen.
Working Smarter with Technology
“Technology is everyone’s best friend when it’s working, but if you don’t stay up to date and reevaluate where you are as a business, it can become a slippery slope and take a while to get where you want to be,” Stearns says.
To that point, he says that Bergquist reviews their supply and product line regularly, including testing products, “doing the homework,” so customers can be secure in their products. Keeping up with technology includes the recent implementation of a new ERP operating system to identify and manage changes in the supply chain.
This project, as with their others, included a lot of communication with customers, vendors and suppliers, so there were no surprises while the company ironed out kinks in the new system. Questions or requests for information were responded to quickly because the customers had been forewarned.
The new operating system allows Bergquist to input information about safety stock volume and helps to better manage inventory levels. It will track shipping trends and alert the company when lead times are slowing down or becoming sporadic.
“We didn’t know what we didn’t know when the pandemic hit,” Stearns explains. “We are starting to see lead times come back to where they were. We adjusted or adapted to the supply chain, we are starting to see our inventory come back to a normalized level to what we like it to be. There are still certain items that we may be carrying more of or having more on hand, because we want to be able to provide whatever item our end customer wants. We want to have stock, so they don’t need to wait.”
The new system helps the company better understand what inventory it needs to stay competitive. Often, Stearns explained, they will place a large order, with some of the materials arriving in the anticipated lead time and the balance further out. When products begin to fall outside of the norm for deliveries, they can follow up, adjust and adapt.
In an ever-changing supply chain, Stearns believes you need to be “more proactive than reactive.” As an example, he describes a situation where the company might have enough of an item on hand for a year’s worth of orders based on past sales. A glitch in the supply chain – or a rumor of one – could see an increase of orders from their customers for that product. The new system would alert Stearns to the higher demand as well as shipping delays, so he could adjust the company’s orders and supply level. It would all be managed, he insists, not simply through the system. There would be outreach to the vendor, the carriers and the customers.
“The supply chain is always changing. You have to adapt and survive and be as proactive as possible with the information you have. That’s where relationships and communications go a very long way,” he said in conclusion. “we’re in a world where that doesn’t always stick. It’s ever-changing, and everyone wants everything right now. But it has to start somewhere, and it all goes back to communications and those relationships. We’ve built where we are today off of that.”
Related Posts
Why Quality Matters in Your Biofuel Blends
Posted on June 25, 2025
HEAT Show Gears Up
Posted on June 25, 2025
What’s Next in Boiler Technology
Posted on June 25, 2025
How Intelligent Are Your Integrated Customer Platforms?
Posted on June 25, 2025
Enter your email to receive important news and article updates.