All
Diesel Engine Underperforming?
by Gary Pipenger, President, Amalgamated, Inc.
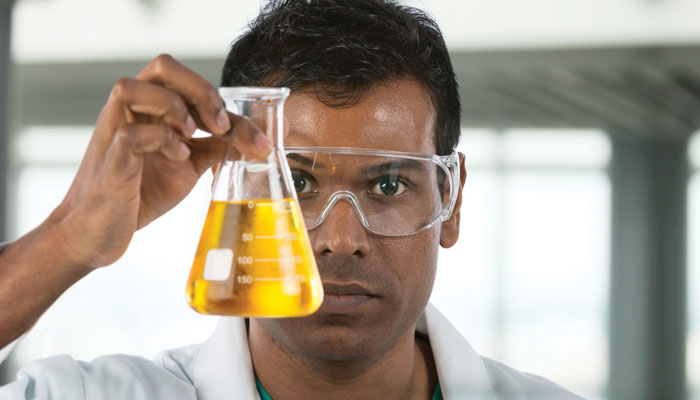
Before every oil refiner in America comments negatively on the title of this article, allow me to clarify that nearly all of the diesel fuels produced by today’s refineries do meet the required ASTM D-975 specification. Unfortunately, the specification has various shortcomings relating to older engines as well as today’s newer technology common rail fuel injection engines.
Add to that the fact that some diesel fuels sold today are not composed solely of the pure diesel fuel as originally refined. This is true because many originally manufactured diesel fuels are mixed and blended with other diesel fuels prior to finding their way into the fuel users’ tanks.
Blending No. 2 diesel fuel with lighter distillate No. 1 and/or kerosene is a common practice conducted by refiners and intermediate terminal storage facilities as well as fuel suppliers and distributors during the cold months. While many believe this is a viable method of reducing winter fuel operability issues, it is not the best winterization technique: It is expensive (for customers), and it changes the physical parameters of the product.
While these changes may appear as a positive for the fuel supplier, they most often are negatives for the fuel user, because they cost the consumer money and provide fuels with poorer physical fuel components for the engines to burn. Less than satisfactory diesel fuel physical properties during the winter months result in changes to the fuel distillation temperatures, lowering fuel BTU energy contents so that engines consume more fuel.
Finally, while these less than optimum diesel fuels will burn and propel the diesel-powered vehicle, just moving the equipment may not be acceptable to the driver. With lower power production, the driver unconsciously tries to make the equipment perform as expected by increasing throttle settings and shifting into a lower gear for more power output. Both of these reactions increase fuel consumption and raise operating costs.
What Is Wrong With Today’s Diesel Fuels
It is well known that changes in diesel fuel and diesel engine technology in Europe happen years ahead of those in the United States. Therefore, most of the chemical additive improvements to “fix” diesel fuel and enhance diesel engine performance for the last 50 years have their roots in Europe. These facts should be expected, since Europe transitioned to diesel fuel power many years before the United States, while America predominantly traveled the gasoline powered developmental road until this past decade.
The biggest problem with today’s diesel fuels in America stems from the fact the diesel engines today need higher performance parameters than are actually produced in diesel fuels. USA diesel fuel product specifications and performance have not kept pace with diesel engine developments.
This situation is the result of the heavy influences of major oil producers within ASTM and the compromises instituted in ASTM diesel fuel specifications made to appease these petroleum refiners. Not to imply there is no equipment manufacturers’ representation or actual fuel users within ASTM, but when fuel quality specifications are discussed, petroleum producers generally wield the greatest influence.
Let’s Talk Specifics
The newer Common Rail Fuel Injection (CRFI) diesel engine systems are designed with component parts that have extremely small tolerances, and these systems operate with exceptionally high pressures. CRFI systems designed since 2007 cannot tolerate even the smallest amount of fuel contamination (or water), and they must be kept exceptionally clean and properly lubricated at all times.
These two conditions demand better quality, cleaner diesel fuels with increased Detergency and improved Lubricity values. Unfortunately, the ASTM D-975 specification does not include a Detergency requirement, and the current Lubricity specification has not been upgraded since 2007. Diesel fuel producers refuse to voluntarily incorporate fuel additives that would protect CRFI engines, and the U.S. government does not legislate consumer protection directives regarding diesel.
Additionally, the ASTM D-975 parameter for fuel combustibility (Engine Cetane Number) has not been changed in over 50 years. Despite the fact that the European diesel fuel specification has been constantly upgraded over time to today’s mandated 51+ minimum. Even though Europe is expected to mandate a 55+ in 2018 or 2019, the U.S. specification requires only a “minimum 40”.
The current low Engine Cetane Number specification in America is more economical and profitable for the refiners and diesel fuel suppliers, while the fuel consumer’s needs are neglected. Today’s high performance engines demand higher Engine Cetane Numbers in order to provide optimum combustibility and maximum fuel economy with minimal unwanted emissions.
Stability and Deposits
Another deficiency in ASTM D-975 is the lack of definition of Storage Stability and Deposit Modification. While these two topics are difficult to define, they should be seriously addressed. It is a fact that after refining, diesel fuels (as organic hydrocarbons) naturally degrade over time. This process of oxidation degradation leads to an increase in fuel system deposits. Free carbon particulate, tank sludge and varnish formations are three of the most common traits.
None of these common occurring conditions are good for the CRFI engines or the pre-2007 diesel engines, and all will cause major operability problems for the diesel equipment operator. Again, while there are available fuel additive chemistries to properly stabilize and protect diesel fuels during long-term storage and eliminate (or greatly minimize) fuel-related deposits, nothing (to the author’s knowledge) is being done at ASTM to mandate incorporation of such solutions into ASTM D-975.
Finally, although ASTM has attempted to address winterization of diesel fuels, the solutions written into ASTM D-975 fall short in many areas when really frigid weather occurs, especially with regard to keeping the paraffin wax suspended during cold temperatures. Although ASTM D-975 attempts to help the diesel fuel user with “suggestions” for winterization testing, nothing (other than a complicated 10 percentile temperature discussion) is done in the specification to mandate the fuel producers or fuel distributors to provide fuels that would guarantee operability for the buyer’s equipment during expected winter applications.
This is especially true with diesel fuels containing unusually high amounts of moisture (i.e. more than 150ppm of water), despite the fact that ASTM D-975 allows 5000ppm of water and sediment to be delivered in the fuel. It should be noted that one of the biggest problems with CRFI engines is the salt deposits that build up internally in the fuel injectors from the typical moisture content, usually less than 150ppm, found in today’s diesel fuels.
There are solidly proven winterization chemical additives (including effective moisture de-icer agents) that can be incorporated into diesel fuels at very economical costs in order to guarantee winter operability at cold ambient temperatures in North America. Unfortunately, ASTM refuses to mandate their use, and the solution is left to the marketplace to sort out with absolutely no policing of the marketed claims of the individual fuel additives offered for sale to the public.
This has led to an enormous amount of fuel additive “marketing fluff,” misrepresented claims, exaggerated performance benefits and bold-faced lies presented to the diesel fuel buyer. This leaves a bad taste in the fuel additive buyer’s mouth and distrust of even the legitimate diesel fuel additive supplier.
Could ASTM International Help?
While it is understood that the scope of ASTM International’s responsibilities does not necessarily include the mandating of any specific fuel additive company’s products, the ASTM organization “could” require stronger language within the specification that would encourage the diesel fuel user to use diesel fuel additives that correct the deficiencies. Along with such encouragement, ASTM International “could” admit that ASTM D-975 does have limitations with regard to guaranteeing the most efficient and proper operation of diesel engines during all types of weather conditions.
Additionally, ASTM International “could” strongly recommend the diesel fuel user test the prospective fuel additives in order to verify the marketing claims before purchasing these products. There are quality formulated fuel additive chemical products that can correct nearly all of the shortcomings of diesel fuels. The buyer just has to look for them and be diligent about investigating, testing and verifying the performance claims made.
All legitimate diesel fuel additive suppliers will provide product samples for testing to prospective customers. The diesel fuel buyer should then have an in-depth laboratory testing program set up with a qualified petroleum laboratory testing facility (one that specializes in and has experience in ASTM D-975 testing) to prove or disprove the marketing claims made by the fuel additive supplier.
Again, this detailed laboratory testing should be done before buying any diesel fuel additive products. This laboratory testing should also be done on more than one specific unadditized base diesel fuel (at a minimum two different fuel samples with varying Cloud Points should be tested) and ideally on the diesel fuels the fuel additive buyer expects to use in his equipment.
Here is a list of some of the physical property improvements the diesel fuel buyer should be looking for to enhance the quality and performance of the diesel fuels purchased:
(a) Cetane Improver to increase the Engine Cetane Number to 50+;
(b) Detergent chemistry to achieve a DW-10 Detergency Rating in all fuels;
(c) Lubricity Agent to lower the HFRR fuel lubricity to 400μm or less;
(d) Storage Stability to slow natural fuel degradation for 12 months or more;
(e) Deposit Modifier to clean off existing deposits and minimize future fuel related deposits;
(f) Cold Flow Improver to lower the Cold Filter Plugging Point (CFPP) by 25 degrees F or more;
(g) Wax Dispersant to fully suspend the paraffin wax 25 degrees F below the Cloud Point;
(h) De-Icer Agent to reduce the moisture freeze point to – 40 degrees F or more.
If the right chemistries are compounded and treated correctly, more than 90 percent of all diesel fuel combustion issues and nearly 90 percent of all unburned hydrocarbon and related emissions at all operating levels will be eliminated. The other 10 percent can be directly targeted by specific chemicals compounded into specialized diesel fuel additive products for the individual application.
Finding the right diesel fuel additives is not easy, but the rewards of less fuel-related maintenance headaches, a cleaner environment, longer equipment life, reduced driver complaints and much better fuel economy/efficiency (fuel savings) are more than worth the effort.
Related Posts
Northeast Liquid Fuel Providers Put Higher Bioblends in Focus
Posted on August 19, 2025
Lower Carbon Lineup Puts Businesses on the Path to Net Zero Goals
Posted on August 18, 2025
Go With the Flow
Posted on July 28, 2025
Why Quality Matters in Your Biofuel Blends
Posted on June 25, 2025
Enter your email to receive important news and article updates.