All
Checking the Boxes with Polypropylene Venting
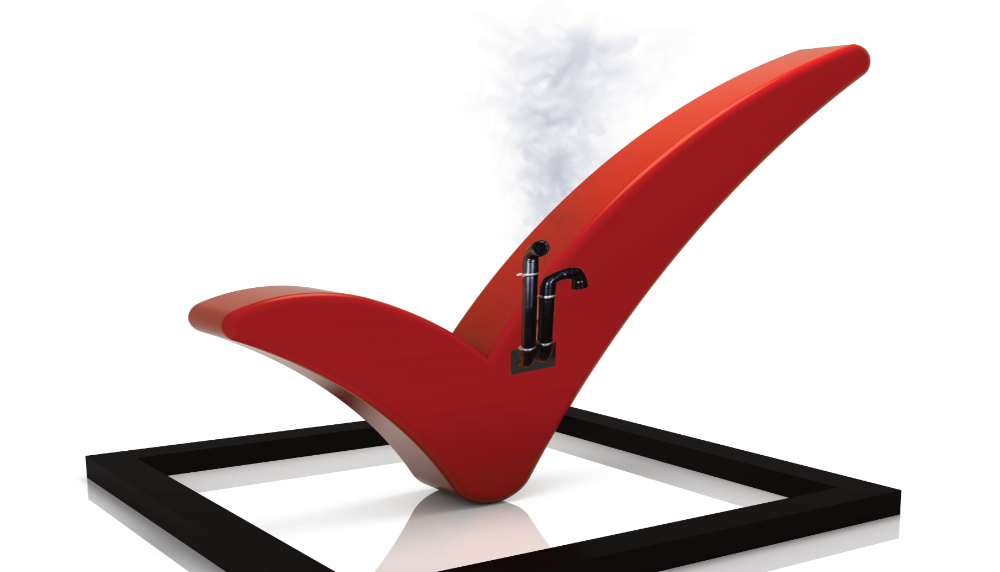
Why one boilermaker calls the technology a “game changer” for the competitive residential installation market
How often does the gas industry provide a pathway to success for oilheat? Here are two examples: low-temperature, durable, and easy to install venting materials and dilution air venting are both well established, reliable and now available for the oilheat industry.
When you were a kid, did you ever go up and down your block what seemed like a hundred times, spending hours on hours looking for something, only to find it as soon as you moved your search to the next block over?
You could say that’s how America’s oil-fired boiler market came to adopt technological innovations like dilution air and polypropylene venting as solutions to make high-efficiency, non-condensing installations easier and more cost-competitive.
“When we originally introduced the Resolute™ boiler line nine years ago, we offered stainless steel venting,” says Roger Marran, president of Lebanon, New Jersey-based manufacturing company Energy Kinetics. “We took a page out of the water heater playbook and used dilution air to further reduce an already low stack temperature. This allowed us to develop a very clean light off and very clean burning oil- and gas-fired boiler, with UL approved polypropylene venting.”
The latter innovation has come to help heating oil contractors check the boxes on two of the most important items homeowners look for when considering equipment and fuel choices: ease of installation and affordability. However, before we get to these benefits, it’s worth exploring how boilermakers arrived at this point in the first place. In other words, before turning right to the next block over, what did they find on home turf?
***
In Energy Kinetics’ experience, one major benefit of the transition from No.2 heating oil to ultra-low sulfur heating oil and renewable liquid heating fuel has been a reduction in equipment and venting issues related to fouling and service.
Higher efficiency operation could cause condensing, and the corrosive sulfur and condensate made equipment and venting operating under these conditions very unappealing. In the days before ULSHO became standard, Marran says, the company had explored an “educter” dilution air vent system with the National Oilheat Research Alliance, which would allow higher efficiency without condensing flue gases as a pathway to reliable long-term operation.
“The challenge was it couldn’t stand up against wind loads of over 40 miles per hour,” Marran says. Dilution air mixed directly in the vented flue gas stream — as used on higher-efficiency water heaters — allowed for full fan capacity, which enabled the boiler to withstand any wind loads.
This innovation allowed heating oil equipment installers to check the boxes on cleanliness and continued operations. But there was still the question of how to bring down installation and service costs, especially for homes with complicated chimney systems and other structural issues. An answer awaited in polypropylene venting.
“If you have older housing stock and need to reline a chimney, or the chimney itself isn’t structurally sound, now you can go out the sidewall and use polypropylene,” Marran says.
Just as dilution air resided a block over in the water heater market, polypropylene venting was already widely used across Europe and in America’s gas-fired boilers. But when heating oil contractors who were familiar with the chore of relining stainless steel chimneys found out that a polypropylene alternative was available, the choice for many of them became clear.
“Once we offered stainless steel and polypropylene as venting options, contractors quickly migrated to polypropylene,” Marran recalls. “Flexible polypropylene chimney liners offer an alternative to stainless steel liners, with comparative ease of installation, especially in tighter or more complex chimney applications.”
***
Indeed, chimney work can be such a headache that many contractors, if given the option, choose to forgo it altogether. One workaround comes in the form of sidewall venting. As the first American boiler company to offer oilheat sidewall venting, Energy Kinetics recognized the potential of this technology early and has been working to improve on it, according to Marran.
“Sidewall venting offers a solution that requires less labor and fewer materials than a relined chimney,” Marran says. The downside is that typical oilheat sidewall venting tends to be noisy. Dilution air and polypropylene both make for quieter operations, as the fan is not mounted at the wall, so it is more isolated and quieter in the home. Also, the chimney can be used as a chase way for flexible polypropylene, if sidewall venting is not desired.
With living spaces shrinking, noise is becoming even more of a factor in homeowners’ equipment-buying decisions. “More homeowners are finishing basements and mechanicals rooms, so the equipment can be closer than ever to living spaces,” Marran explains. “Quiet operation is no longer an option, but a requirement in these cases.”
***
Why polypropylene venting and not PVC? The answer might be obvious to contractors who are experienced with both materials, but for comparison’s sake, let’s check some more boxes.
“Whereas polypropylene is lightweight and can be easily installed as a one-man job with just a few hangers, PVC is heavier and comes in 10-foot lengths, which can take two people to support and install in the same application,” Marran says. “Polypropylene also has the security of a high-temperature, solid joint retained by a locking ring – just slip the end in and click it in place. PVC is reliant upon a cement-only joint.”
This also makes polypropylene venting easier to service. Though the polypropylene vents’ lock rings provide resistance of up to 100 pounds of force, a technician can easily unlock and disconnect them when fittings or piping need to be inspected. On the other hand, cement-sealed PVC would need to be cut apart and replaced, which often requires the addition of couplings. It’s a labor intensive process that yields unfinished results.
Not to mention: due to its low temperature rating, PVC isn’t even code-compliant for venting boilers in New York City and several other jurisdictions. “PVC has a maximum operating temperature of 140∞F to 149∞F, but boilers often operate above 180ºF for hot water and heating,” Marran explains. “Polypropylene has a temperature rating of 230ºF for gas and 248ºF for oilheat, and more attractive vent termination options than PVC or typical oilheat sidewall vent systems.”
Energy Kinetics sees the development of the Ascent™ Combi and Ascent™ Plus Combi boilers as a major milestone for the company. Likewise, the Resolute™ RT marks the “next generation” in Energy Kinetics’ Resolute™ boilers. Polypropylene venting compatibility is one of several innovations that land these systems on the cutting-edge of oil-fired boiler technology. So, what’s next for Energy Kinetics and boiler technology in general? For a glimpse, Marran returns to the subject of water and a challenge that’s all too common in some regions – namely, hard water. “We’ve got some interesting technology coming down the pipe to provide better options for making hot water in buildings with hard-water issues,” Marran says. “We’re still in the R&D phase, but it looks very promising.”
Related Posts
From Blue Flame to Biofuels
Posted on June 25, 2025
HEAT Show Announces Fenway Park Backyard BBQ
Posted on May 15, 2025
Delivering New York City’s Clean Energy Solutions
Posted on May 14, 2025
Are You a Leader or a Boss? The Choice is Yours
Posted on May 14, 2025
Enter your email to receive important news and article updates.