All
Airflow Management in Tight Homes
by Shawna Henderson, Blue House Energy
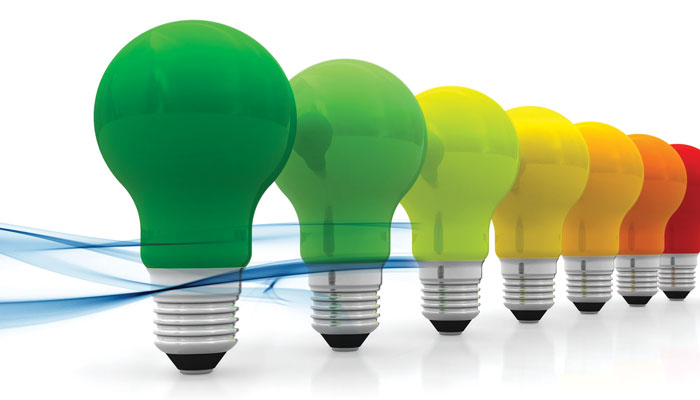
Manufacturer develops low-airflow systems that run in long cycles
By Shawna Henderson, Blue House Energy
Here’s one fact that can’t be argued: Continuously improving the thermal envelope requirements (as per building code or beyond) results in tighter houses with efficient ventilation systems. Here’s another one that’s also indisputable: Standards that were written 20+ years ago need to be revisited and brought up to speed to reflect current building science, construction standards and equipment efficiencies.
Industry capacity and good practice in new construction have improved over the past 30 years to the point where major production builders are offering Near Zero Energy and Zero Energy Homes as a matter of course. These houses rely on airtight envelopes and mechanical ventilation to keep energy bills low and occupant comfort and health high.
The problem is, for cold climate housing the standards for sizing space-conditioning equipment don’t match up with the way airtight, highly insulated envelopes perform. The result is often higher-than-expected energy bills and complaints from occupants about cold rooms in their new houses.
This has changed in Canada. In 2013, an updated version of CSA F-280 (Determining the Required Capacity of Residential Space Heating and Cooling Appliances) was brought into play for Canadian homes.
This is serious and exciting. Even as it was first being written in 1990, critics were flagging problems in how F-280 dealt with air leakage and ventilation. In the period prior to 1990 when the standard was being developed, heat recovery ventilators (HRVs) were unheard of, and glazing options that are now code-required were not available. Tighter building envelopes and mechanical ventilation were addressed in the original version, but only in the appendices. The problem as the industry moved forward has been that under the 1990 version of F-280, air leakage and ventilation accounted for 40 to 50 percent of the overall design heating load.
Updating the Code
The new version of F-280 takes tighter envelopes and mechanical ventilation into consideration and changes the game for equipment sizing. So what’s the overall impact? Here’s an example comparing the old and new F-280 standard that Gord Cooke, president of Building Knowledge and well-known trainer, included in an article in Builder News (Winter 2014) using a 2-story, 2200 square-foot home, built in Newmarket, Ontario to current Ontario Building Code.
Total Heat Loss Btus/hr | Air Leakage Component of Heat Loss Btus/hr | Total Heat Gain Btus/hr | |
CSA F-280 (Old) | 55,425 | 13,225 | 31,250 |
CSA F-280 (New) | 33,875 | 4,020 | 26,150 |
Under the new standard, the total heat loss is reduced by nearly 40 percent, while the total heat gains decrease by 15 percent. The old standard anticipated the air leakage component for this house making up 24 percent of the total heat loss. Under the new standard, it is less than 12 percent.
The new standard means significantly smaller heating requirements, which means smaller heating units. The market can currently supply units down to 40,000 Btu/hour. But in a cold climate, anything smaller than this example house is going to have a heating load far below the capacity of existing equipment. Design heat loads for condos and other multi-unit dwellings will be even smaller.
According to Doug Tarry, an Ontario builder who has been working with manufacturers and building officials to demonstrate the benefits the new F-280, the new standard validates what high-performance builders have been seeing for years: High efficiency units in houses with low heating loads often cannot meet homeowner expectations when it comes to comfort levels.
Why is this? Comfort problems stem from the mismatch of furnace capacity and heating loads. Houses with oversized furnaces will experience cold rooms due to short cycling, because the units don’t run long enough to get adequate heat flow to all rooms in a house.
Gord Cooke says the changes to F-280 will result in significant improvements to the comfort levels of cold climate housing, as code requirements continue to improve the building envelope. He also notes that the “cold room” syndrome isn’t as much of a problem in milder climates, because the rates at which rooms cool down aren’t as drastic as those in the northern U.S. and most of Canada, driven as they are by wide temperature differences between indoors and outdoors.
Equipment Solutions
In anticipation of the changes to the F-280 standard, Canadian manufacturer Dettson, well known for their oil-fired equipment, charged ahead with an innovative program to match up gas-fired equipment with the new standard and the needs of high-performance house construction. I got my first look at Dettson’s system this year, at the Canadian version of Spring Training Camp that was hosted by Gord Cooke and Tex McLeod.
In 2011, Dettson focused on developing very small capacity, high-efficiency gas furnaces with variable speed motors that were quiet enough to be included within the living space of a smaller, high performance house. They worked with more than 50 gas utilities in the U.S. and in Canada and consulted with building scientists, installers and builders to determine how best to deliver year-round comfort to occupants in the most efficient manner. Their goals were: better controls, a smaller footprint, less noise, more comfort.
Dettson launched its “Right Sized System” in 2014, featuring a small capacity gas-fired furnace that modulates between 40 percent and 100 percent of the unit capacity, meaning that on their modulating 15,000 BTU/hour Chinook unit the range of capacity would be 6,000 to 15,000 BTU/Hour. In 2015, Dettson added a heat pump to the system, matching the furnace’s low capacity, modulation and low air flows for cooling needs. Improvements to the control system added the HRV/ERV into the mix to allow for continuous comfort levels with very low CFM. This year, Dettson has also added a modulating low-capacity electric furnace to their product offering.
This system is an interesting variation on the bivalent heat pump system (that I wrote about in the May issue of Oil & Energy), where heat pumps are used to carry existing oil-fired systems through shoulder seasons and supply cooling needs.
But here’s what’s really interesting from a building science perspective: The low-capacity modulating furnace runs for several hours at a time (3 to 10, or even more) with very low air flows. It seems counterintuitive to think that you can run a furnace for hours on end and have it remain efficient, and at the same time have air flows that range from 180 to 300 cfm in a typical 2,000+ square foot house. Not to mention the effect it might have on the occupants in terms of noise levels. But the proof is in the monitoring.
Testing was carried out in Pittsburgh on a house fitted with 300 sensors to simulate the living habits of two adults and two teenagers. The installed heating capacity was undersized for the house, but even during the times that were well below the design heating temperature for the area, the modulating furnace didn’t go above 90 percent capacity. In fact, for most of the very cold winter of 2014, the furnace ranged between 60 and 90 percent. Over a 48-hour period in the winter the furnace ran continuously, the airflow ranged from 180 to 300 cfm.
Monitoring of Doug Tarry’s “Discovery Home” in St. Thomas, Ontario, showed that, through the long, hard winter of 2014, the Dettson furnace (sized to the new F-280) did not exceed 60 percent of capacity. That is: It did not push past 18,000 Btu/hour. Again, monitoring showed that the furnace ran for long cycles, keeping a steady but low flow of warm air moving through the house.
Stable Humidity Levels
A very interesting result of another monitoring program at Dettson was a comparison of relative humidity (RH) and temperature differences using thermostat setbacks. There was up to a 7 percent change in RH when setbacks were used, as opposed to a 2 percent change in RH where no setbacks were used. This change in RH levels, especially in basement areas, can make enough difference to cause condensation and resultant mold growth where none would have been present before.
Once the heating side of the system was dialed in, the push was to provide a cooling system that would match the furnace by operating on longer cycles with lower airflows. The Discovery House in St. Thomas, Ontario was fitted with an Alizé 1.5 ton heat pump. The heat pump runs at 180 to 300 cfm and operates for 3 to 10 hours in a cycle. Monitoring shows that the unit ran at no more than 55 percent of its operating capacity during the cooling season.
The controls were improved to interlock with an HRV or energy recovery ventilator (ERV), so that the mechanical ventilation runs at similar speeds when there is no cooling or heating requirement. This keeps the air moving and evens out temperatures throughout the house.
The last piece of the puzzle that Dettson tackled was the delivery. You can’t run on low air flows if you have leaky ductwork. The fact that conventional ductwork (inside the conditioned envelope or not) can have more than 40 percent air leakage is one of the reasons why forced air systems are designed to deliver a lot of air. Even ductwork that is considered ‘well sealed’ can experience 15 percent air leakage. Modelling and testing different kinds of systems led to Dettson creating a distribution package that uses an 8” round trunk duct with 2½” flex ducts leading to supply grilles. Testing shows air leakage in this type of assembly can be held at about 2 percent.
I haven’t done an in-depth study of other low-velocity forced air systems that use small diameter ducting. A quick online search shows only high-velocity forced air delivered through small ducting. How is the market responding to this innovative package? In a phone interview, Dettson’s General Manager, Marc Chenier, listed several production builders across Canada and in every U.S. climate zone that are taking on their heating/cooling/controls/ductwork package.
I’d be very interested in results from a retrofit project that used this type of system. While the monitoring that Dettson has carried out looks good for new construction, it remains to be seen if there are opportunities for existing housing What are the roadblocks?
There is so much room for innovation as we dial in the high-performance house. Expect more useful innovations in the years ahead.
Related Posts
New Burners Take on All Fuels!
Posted on July 28, 2025
From Blue Flame to Biofuels
Posted on June 25, 2025
HEAT Show Announces Fenway Park Backyard BBQ
Posted on May 15, 2025
Delivering New York City’s Clean Energy Solutions
Posted on May 14, 2025
Enter your email to receive important news and article updates.