All
AFUE Misses the Mark on Boiler Efficiency
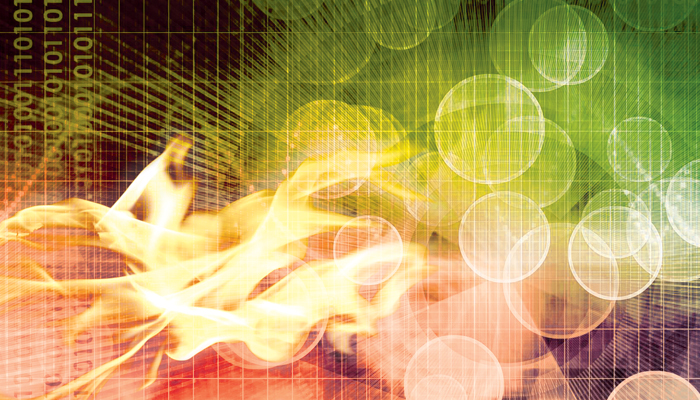
This article originally appeared in the November 2006 edition of Oil & Energy. A follow-up appears in the May 2019 issue.
The U.S. Department of Energy’s (DOE’s) Annual Fuel Utilization Efficiency (AFUE) rating system is often criticized for failing to measure the true efficiency of hydronic heating systems. Among its flaws, AFUE omits combined heat/hot water systems, which are in widespread use.
One prominent critic of the AFUE measure is Roger Marran, executive vice president of Energy Kinetics, in Lebanon, N.J., maker of the System 2000 combined heat/hot water system. Marran recently fielded questions from Oil & Energy about the AFUE rating system.
According to Marran, AFUE was developed to test warm air systems. “When DOE was required to come up with an appliance efficiency rating for home heating equipment in the late 1970s, they turned to a Honeywell program that evaluated the seasonal efficiency of furnaces,” Marran said. “In their expediency to develop a boiler efficiency standard, they adapted the basic concepts of the furnace efficiency tests, which totally ignore many of the characteristics of heating systems using boilers and especially those where the boiler supplies both heat and domestic hot water.”
He added. “The resulting AFUE of both furnaces and boilers is very close to steady-state combustion efficiency and while reasonably accurate for furnaces, it is totally misleading for boilers, especially oil units that usually also make domestic hot water.”
A Better System at Brookhaven
Marran noted that the DOE’s Brookhaven National Laboratory (BNL) had been working on a better system for years. “Prior to the DOE establishment of the AFUE procedure, BNL had been performing input/output tests on oil-fired boilers that measured the energy delivered to the home for heat and hot water. Their cycle tests, which included evaluation of standby losses, provided a much more accurate measure of seasonal efficiency. These tests indicated seasonal efficiency because of jacket and standby losses were 12 percent to 30 percent below steady-state combustion efficiency.” Marran said. “DOE ignored this data and continued with their furnace-adapted standard for boilers, which is in effect to this day.
“Of interest, the Brookhaven procedure accurately predicted that the upgrading of burners to the high-speed retention design would save a typical 16 percent on annual fuel consumption. This documentation resulted in the upgrade of many thousands of homes and a tremendous energy saving for the country. This prediction would not be possible under the current AFUE test procedure.”
Marran discussed the kinds of problems that the AFUE rating can create. “Most manufacturers are comfortable with AFUE for boilers since it does not require any innovation other than modifying units to obtain higher steady state combustion efficiency. Interestingly, removal of insulation actually improves the AFUE rating by increasing jacket losses not accounted for in the procedure; this results in a lower stack temperature and the higher rating, which measures stack loss only,” he said.
“Energy Kinetics and a few other organizations, such as the American Council for an Energy Efficient Economy (ACEEE) and the New York State Energy Research and Development Authority (NYSERDA), have been the only parties who have consistently worked for an improved procedure that would accurately provide homeowners with valid information on potential savings” when comparing systems. NORA recently joined efforts with NYSERDA and funded renewed input/output testing at BNL.
“Initially, we had to rely on the original Brookhaven input/output data, and field results of our earliest System 2000 models, which indicated the significant seasonal energy savings in comparison to all tested products on the market during the early 1980s. Brookhaven was prevented by DOE, who controlled their budget, from performing further input/output tests through the 1980s and 1990s as they were in conflict with the ‘national standard’ as set by DOE.”
Marran continued, “Marketing has been hampered by the AFUE procedure in that virtually all manufacturers have boilers with 86 percent to 87 percent AFUE ratings, which, if tested under the input/output method, would have significantly lower ratings (typically 12 percent to 30 percent lower).”
AFUE Misses Efficiencies
Energy Kinetics’ flagship appliance is the type of system that is undervalued by the AFUE system, according to Marran. “System 2000 design evolved from analysis of the early Brookhaven test data using the input/output method. It predicted significant energy savings if standby losses could be reduced. System 2000, as a boiler, has been designed with minimal thermal mass (160-pound boiler with only 2.5 gallons of water) and controlled to run like a furnace. It does not require a draft regulator for proper operation. It is only fired on demand, and at the end of any call for heat, its low mass design permits recovery of energy from the boiler to the house or to the domestic hot water tank until the boiler is cool, which virtually eliminates all standby losses. The design also minimizes jacket, tank and flue losses.
These measures may help with true seasonal efficiency, but they are discounted by the AFUE standard, Marran said. “These gains are major compared to conventional boilers that maintain temperature. Because AFUE does not include these losses in reducing the rating of conventional equipment, we are unable to use our improvements in obtaining higher AFUE ratings, which would be appropriate if true seasonal efficiency were the objective of the AFUE rating procedure.”
The DOE can improve its methodology, according to Marran. “The input/output method in development tests at BNL under a contract with NORA and NYSERDA, using modern computer data acquisition systems, appears to be the answer for a new, improved rating system that will provide consumers with ratings that will closely approximate in-home performance and potential savings.
“A significant output from this program and its data is that standby losses are a major contributor to energy waste and these losses increase rapidly as the heating systems are oversized relative to the actual heat loss of a home. This is particularly true in the case of tankless coil boilers, which are frequently fired at high rates to permit their instantaneous delivery of domestic hot water. Since the AFUE method does not recognize any hot water-making performance or summer operation, these huge standby losses are ignored in the AFUE test procedure.
“Hopefully, the input/output test method can be recognized in the near term as an appropriate rating method and allow this industry to move forward with energy conservation by replacing outmoded and inefficient equipment.”
System 2000 Was Born in a Traffic Jam
Oil & Energy asked Marran to explain how John Marran developed the System 2000. “John was working for a Swedish heat transfer and fluid handling company in 1978 when his family at Marran Oil on Long Island approached him and suggested that he design a new kind of boiler. The oil crisis was in full swing and people were looking for a way to cut their energy costs. John thought it would be an interesting project and began to brainstorm.
“The ‘aha’ moment came on a tedious drive from Long Island to his home in New Jersey. As anyone who knows Long Island can tell you, the Long Island Expressway has a tendency to be backed up and is frequently called the world’s longest parking lot. As he slowly inched forward along the congested road, he suddenly thought, ‘What would happen if I took an oil burner and wrapped a spiral heat exchanger around it?’ As he sat in traffic and continued his journey home, he designed the project in his mind. By the time he got to the door of his house, he knew exactly what he wanted to do. He immediately called the service manager at Marran Oil and asked him if he could quickly get hold of a few pieces of steel in particular dimensions. He and John arranged to meet him on Long Island the next day.
“When John arrived at Marran Oil, they took two pieces of steel and wrapped them with an oil truck hose reel. They welded two plates together and put them into the now well-known coil shape of System 2000. Unfortunately, on this very first prototype, the welding was not expertly crafted and it leaked. To stop the problem, they dumped a can of oatmeal into the boiler to plug the leaks. Once the leaks stopped, John ran some tests. The results were amazing. He knew he was on the right track.”
- Runs only on demand.
- Low thermal mass, heats up and cools down quickly.
- Return temperature at room air temperature
- Return air minimizes jacket loss, but jacket losses are considered a loss
- Have cooldown cycle which eliminates off-cycle standby losses
- All measurements of efficiency are of flue losses only
- Low combustion air and draft regulator losses because chimney cools after each cycle
- AFUE equals combustion efficiency and is a reasonable comparison
- Burner cycles frequently to maintain temperature 24 hours a day. Test procedure assumes on-demand only operation and omits standby losses.
- High thermal mass (500 lbs. cast iron and 8 to 10 gal. water content). Heavy iron and large water content heats slowly and leaves energy wasted in the boiler when the burner shuts off.
- Return temperature typically 1600 but AFUE test procedures are performed at 1200, allowing higher test efficiency.
- Jacket loss a function of insulation and boiler standby temperature. Jacket losses, running and in standby, are considered a gain to the home. (Also see #7)
- Have significant off-cycle losses through hot boiler, up the chimney and from the jacket, not properly detected in the lower temperature test procedure.
- All measurements of efficiency are based on flue losses only during a short single cycle and do not measure those that occur during many hours of standby operation, especially summer.
- High room air losses through the unit and draft regulator because chimney stays warm creating chimney draft.
- AFUE equals combustion efficiency. Real seasonal efficiency is 12% to 30% lower making AFUE a meaningless and misleading comparison.
Related Posts
Why Quality Matters in Your Biofuel Blends
Posted on June 25, 2025
HEAT Show Gears Up
Posted on June 25, 2025
What’s Next in Boiler Technology
Posted on June 25, 2025
How Intelligent Are Your Integrated Customer Platforms?
Posted on June 25, 2025
Enter your email to receive important news and article updates.